En el contexto del proyecto de construir el velero Voilier, ver el proyecto aquí en el foro, me había decidido por el uso masivo de electrónica que me hiciera yo mismo. Las razones para esto eran múltiples. Por un lado el velero con un casco de algo más de 150 cm de largo y unas velas bastante grandes requiere componentes más grandes de las que se consiguen en el mercado, o componentes caras en extremo. Un ejemplo de esto es el decodificador de robbe multiprop que decodifica los controles para 8 servos transmitidos por un solo canal de mi F14 Navy. La componente, más de 100,- Euros para el decodificador, es pésimo en lo que a la función del mismo se refiere. Normalmente el receptor R/C en el modelo genera un impulso de entre 1 ms y 2ms para cada canal cada 20 ms. El decodificador de robbe genera cada 20 ms el impulso de uno de los 8 servos y repite este después de 8 ciclos de 20ms, ósea después de 160 ms. El resultado de esto es que los servos se mueven sumamente despacio, con poca fuerza, pues el circuito en el servo requiere que se le aplique el impulso del receptor máximo después de un período mucho más corto.
Usando un controlador mega8, como el que presento en el cursillo electrónico, por menos de 10 Euros realizo un decodificador excelente con útil funcionalidad adicional.
En el cursillo electrónico muestro como se realiza una tarjeta uniendo los pines de las componentes con hilos alámbricos. Después de experimentar con el método de transfer del tóner con una plancha, me decidí experimentar el hacer una placa creando las geometrías usando o un programa dedicado y gratuito llamado Eagle y/o con otro programa gratuito para CAD de 2 dimensiones, Solid Edge Draft. La selección de cual programa uso en cada caso depende del objetivo de la placa. Cuando realizo la placa para un variador para motores DC con escobilla o para motores de paso, Eagle es el programa adecuado. Cuando realizo la placa para las luces para la iluminación indirecta de la cubierta del velero Voilier, Solid Edge es mi programa predilecto, pues me permite con altísima precisión crear las imágenes de las placas. En esta contribución deseo presentar la realización de las luces para mi velero y en este contexto presentar como hago las placas, como aplico el estaño y como hago la soldaduras usando mi horno "reflow" construido usando un horno para pizas comprado en eBay por 25,- Euros.
Aquí la imagen de la placa para la LED amarilla de alta potencia de OSRAM de 19x7 mm!
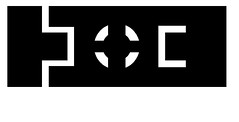
LEDs para montaje en superficie de alta potencia, pueden permitir hasta 750 mA de corriente, generan una gran cantidad de calor que las destruiría rápidamente si no se cuida de usarlas de tal manera que el calor generado sea disipado rápidamente. En el caso de mis lámparas uso una placa foto sensitiva de la empresa Bungard de 70um de espesor de la capa de cobre, el doble de los usuales 35um. El LED tiene 2 pines, uno anódico y uno catódico, y una base para transmitir el calor a la placa por el lado inferior del LED, este punto también está conectada al pin anódico eléctricamente. Por tal razón vemos que la placa a la izquierda está eléctricamente aislada del resto de la superficie de cobre por un canal de 0.6 mm de ancho. El punto céntrico, donde el LED permite disipar el calor, tiene el diámetro de 2,5 mm. Este círculo interior lo he comunicado por 4 puentes al resto del cobre, para así saber exactamente donde aplicar el estaño para soldar este punto y limitar el flujo del estaño al derretirse este, pero permitiendo transmitir el calor. A la derecha el surco en “U” indica la posición del segundo pin del LED, capacitándome así a saber dónde poner el estaño y como posicionar el LED.
Como voy a construir 50 de estas luces, cada una de ellas teniendo que poder ser instalada en su puesto correspondiente, requiero construir un ensamblaje que me capacite lograr que cada lámpara que construya, aunque esto fuera después de años, tenga las exactas dimensiones de todas las anteriores y quepa en cualquiera de los puntos donde estas sean instaladas.
También requiero que el calor que se vaya a crear cuando opere el LED con mucha corriente pueda ser disipado. Por esa razón las placas son soldadas a una ranura de 2x1,75 mm en un listón de latón de 7mm de largo y 5x5 mm a cada lado de la placa. Cada uno de estos listones tiene una perforación de 2,5 mm a la que le corto una rosca de 3 mm de diámetro. Estas perforaciones a ambos lados de la placa tienen que ser posicionadas de forma tan exacta que el conjunto de placa mas los 2 listones pueda ser atornillado a otro listón de latón que a su vez cumple la función de recibir el calor del LED y transmitir este a la estructura de aluminio que conforma la cubierta desmontable del Voilier, ver paso a paso del proyecto aquí y así disipar el calor.
Esta explicación para explicar el porqué la construcción tiene que ser tan compleja.
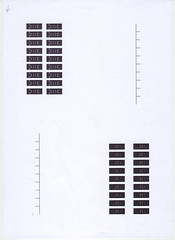
En la segunda imagen vemos como, usando Solid Edge, replique la tarjeta para crear 2 columnas de a 9 placas. Estas caben así en la placa foto sensitiva de Bungard, logrando así hacer un buen uso de esta.
Ahora lo que hice fue imprimir la imagen de las 9x2 placas sobre una hoja de papel A4, usando el máximo de contraste, la selección de papel de alta resolución, para así lograr que la imagen imprimida por mi imprenta MP830 de canon a base de tinta tenga un máximo de opacidad y de resolución para que las estructura finas sean recreadas de forma auténtica y exacta.
Después tome una hoja de folio transparente para impresoras de tinta, corte un pedazo de esta de tal dimensión que la imagen de las 9x2 placas impresas pudiera ser impresas sobre esta y la pegue con cinta scotch sobre la hoja de papel en la posición adecuada. La razón para esto es, que el folio transparente es relativamente caro y que así logro el mejor uso de esta. Pegándola sobre la hoja de papel con la impresión de las placas garantiza que el pedazo de folio transparente se encuentre en aquel lugar sobre la hoja de papel donde al repetir la impresión la impresora pondrá la imagen. Para saber cómo tener que poner la hoja de papel en la impresora, marco con una flecha, se ve en la imagen de lo hoja de papel A4, e introduzco el papel al depósito de papel de la impresora. Después de imprimir la imagen de las 9x2 placas se que en mi impresora la flecha tiene que estar boca abajo y al lado externo del depósito, cuando he pegado el pedazo de folio transparente, l lado áspero del folio es aquel sobre el cual la impresora aplica la tinta, tengo la película que usaré para exponer las placas a la placa foto sensitiva.
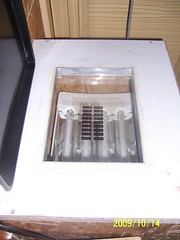
Aquí vemos el pedazo de folio con las imágenes impresas sobre el vidrio de mi aparato para exponer la imagen de las placas sobre la placa foto sensitiva. Un comentario. La calidad de la placa en lo que se refiere a lograr estructuras finas depende mucho de la calidad de la placa foto sensitiva. Mi amigo Torsten uso una placa barata logrando una calidad muy inferior a la que logré yo.
Como fuente de luz utilizo un bronceador para la cara que se consigue por eBay sumamente barato. Torsten lo compro por 1 Euro, yo pague la fortuna de 15,- Euros por un bronceador idéntico! Pueden ver el bronceador debajo de vidrio con el folio. Instalé el bronceador de forma que las lámparas ultravioletas estén paralelas al vidrio y que el control del tiempo pudiera salir y ser usado con el bronceador dentro de la caja. El vidrio lo conseguí de un marco para fotos. Atender que el vidrio no sea esmerilado, pues esto destruiría las claras líneas que deseamos obtener. A los bordes de la abertura puse un marco de aluminio bastante alto y aseguré que el borde inferior tocara el vidrio sin dejar una ranura por medio. La razón para esto es, que por un lado quiero poder usar el marco de aluminio para poder poner las placas y el folio transparente orientándome por el marco y que este no se deformara por el uso prolongado, lo que podría ocurrir si hago el marco de madera. La otra razón es que la tapa, que tiene una superficie de espuma por debajo, al ponerla debido al marco no pudiera descuadrar de forma accidental la placa y/o el folio transparente.
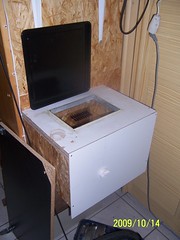
La segunda imagen muestra el aparato con la tapa puesta.
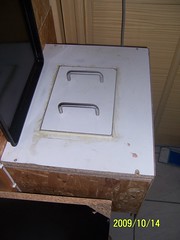
Cuando Ustedes se construyan su propio aparato para exponer las placas foto sensitivas a la luz ultravioleta, tendrán que investigar cual es el tiempo de exposición que el aparato de Ustedes requiera, ya que cada aparato difiere.
Para esto toman una franja de placa foto sensitiva y cubren el 90% de esta con alguna hoja opaca y exponen la placa por digamos 3 Minutos, luego moviendo la hoja opaca exponen un 10% adicional por un Minuto y repiten esto hasta haber expuesto la placa completa. La razón para esto es averiguar, cual es el tiempo mínimo que requiere la maquina que Ustedes se construyen para exponer las placas foto sensitivas que Ustedes usen. Diferencias en la distancia de las lámparas ultravioletas al vidrio, espesor y translucidad del vidrio y dios sabe que otras razones hacen que cada máquina tenga sus valores. Las placas foto sensitivas de Bungard son muy tolerantes a la sobreexposición por lo que mientras expongan sus placas el tiempo mínimo que requieran, 1 o 2 minutos más suelen no ser un problema.
Una vez completada la exposición de la placa la pondremos en una bandeja de plástico por ejemplo que contenga el líquido para revelar las placas. Esto puede ocurrir a la luz normal que tengan en su taller. El líquido se puede almacenar por mínimo 6 meses sin problemas en una botella PET. Importante es etiquetarla claramente para indicar que contiene líquido para revelar para evitar intoxicaciones accidentales. Desafortunadamente no tomé foto de la placa después de revelarla, pero las placas para mis luces aparecían de un color tipo verde.
Atención: Poner el folio (película) con la imagen de las placas de tal forma sobre el vidrio que la tinte este en el lado de arriba y así poniendo la placa foto sensitiva sobre el folio la tinta esta directamente sobre la superficie de cobre evitando así que luz penetre por debajo de la parte opaca y exponga la placa foto sensitiva donde no debe!
Para grabar las placas uso una solución de persulfato de sodio. Esto lo compre en una botella plástica con un polvo blanco, el persulfato de sodio, del que tome la dosis para crear una solución de ½ litro agregando agua corriente. Y he usado la solución 9 meses después de haberla mezclado y aún funciona. Cuando noto que no funciona como acostumbra la desecho. Así el costo es mínimo pues con seguridad 1 soluciones podrá ser utilizadas por un plazo de tiempo entre 6 meses y 12 meses. Esta solución funciona óptimamente a una temperatura de 40 grados Celsius. Para ello uso una bandeja de vidrio resistente al calor, la que pongo sobre una hornilla de gas de mi equipo de camping, poniendo una hoja de lata entre la llama y el vidrio para reducir el estrés al vidrio. Pongo la placa expuesta y revelada en la solución de persulfato de sodio y me quedo revolviendo la solución con un pincel . Cuando no revuelves la solución con el pincel se van creando burbujas de gas sobre la superficie de cobre de la placa.

En la foto ven la configuración. Unas fuertes recomendaciones:
1. Hagan esto no en su taller, sino en un lugar con buena ventilación, pues salen gases de la solución que afectan la salud, irritan en la boca y los labios y los ojos. Aún peor, estos gases son muy corrosivos por lo que pueden dañar cualquier equipo que tengan en el taller.
2. Usen un hornillo más estable, que no se les vaya a voltear, con todas las consecuencias adversas.
3. Usen la ropa más vieja que tengan, pues el riesgo de que les caigan gotas sobre la vestimenta es alta y la solución Dana el tejido creando huecos en este.
4. Yo uso una máscara para evitar inhalar los gases.
La foto no muestra la situación como grabo la placa, pero muestra el equipo que uso con el propósito de ser más informativo.
Como me quedo continuamente pasando con el pincel por sobre la superficie de la placa para mantener la solución en movimiento, después de cierto tiempo la solución empieza a crear burbujas por acercarse a la temperatura de hervir. En ese momento apago la llama del hornillo y continúo revolviendo la solución. Después de aprox. Unos 3 a 5 minutos se nota como la capa de cobre de la placa empieza a oscurecerse y a desaparecer empezando por los bordes de la placa. Este punto por lo general implica que después de cierto tiempo volví a encender el hornillo, pues la solución en esa bandeja se enfría muy rápido, antes de llegar a ver como desaparece el cobre. Mi impresión es que si evito que la solución hierva apagando el hornillo, la temperatura oscilara alrededor de los 30 a 50 grados Celsius cumpliendo su función. Continuo pasando el pincel por sobre la placa hasta tener absoluta certeza que todo el cobre que quiero quitar realmente ha sido quitado por los efectos corrosivos de la solución.
En ese caso saco la placa con una pinza y lavo la placa bajo agua para asegurar que no quede resto alguno de la solución sobre la placa. Esto es el resultado:
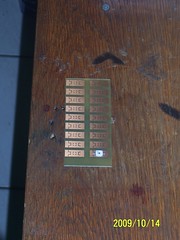
Como pueden ver las estructura finas aparecen en total perfección! es tan sencillo y barato hacer placas de esta forma que no entiendo porque algunos temen usar esta técnica. También pueden ver el LED que puse sobre la placa para demostrar como deberá ser posicionado y soldado en un próximo paso.
El otro paso que hago para crear las placas es aplicarles una capa de estaño usando un producto químico de Bungard llamado SUR-TIN, que consiste de una bolsa con un polvo y una botella con un líquido. Les mostraré esto cuando mis test con las placas haya sido exitoso.
Ahora les quiero mostrar mi horno para reflow:
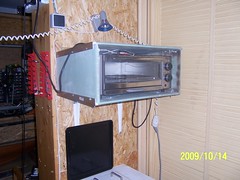
En la imagen pueden verlo como lo he instalado en mi taller. He usado esas placas de aislamiento no inflamables para evitar que el equipo pueda crear un incendio. La placa de arriba esta algo inclinada, de forma que el aire caliente que se genera en el horno abandone la caja por adelante estando así lejos de cualquier objeto que pueda quemar. El horno, como lo escribí antes, lo compre por eBay y es un horno para pizas casero. Escogí un modelo que casi no tiene material plástico para así evitar que el ser sometido al calor en esa caja lo pueda afectar.

Aquí una vista al interior del horno para pizas usado para soldar según el método del reflow.
Reflow es un método de soldar donde se somete la placa y las componentes a una fuente de calor que derrite el estaño. Esta metodología permite soldar componentes modernas que son imposibles de soldar con un soldador clásico. Como la placa y las componentes completas son sometidas al calor hay que tomar en cuenta el estrés que esto representa para las componentes. Como la tecnología es muy usada en el ámbito industrial las hojas de datos de los productores de las componentes por lo general tienen documentado un perfil de temperatura sobre el tiempo que se deben cumplir para evitar dañar las componentes en el proceso. Esto es cuanto más crítico, cuanto más grandes son los empaques. La razón es que las componentes, aún cuando son almacenadas en una bolsa sellada con material absorbente de humedad, absorben una cierta cantidad de humedad. El perfil de calentamiento para soldar según el método reflow, primero calienta las componentes a una temperatura comparativamente baja, unos 130 grados Celsius, y mantiene esta por cierto tiempo. este paso se llama "Baking", u hornear, y seca las componentes bajo la influencia del calor. Luego la temperatura es aumentada hasta un vaolor de aprox. 245 grados Celsius, manteniendo esta temperatura máxima mínimo 10 segundos, máximo 30 segundos para permitir que el estaño se pueda fundir soldando todos los pines de un empaque. 245 grados es la temperatura para un ámbito libre de plomo, unos 220 grados para estaño con plomo, ya que el estaño sin plomo requiere de una temperatura más alta para fundir. Esto también significa que el estrés térmico es más alto cuando se usa un medio sin plomo. En este momento he logrado con éxito fundir el estaño sin plomo, cuando mi multimetro con sensor para temperatura indicaba 242 grados. Tuve grandes problemas antes de llegar a este punto, pues mi fuente usual para el estaño en forma pastosa requerido para este propósito era demasiado vieja y por eso no funcionaba en el horno. Por eso tienen que encontrar un proveedor que les surta con la pasta de estaño y que indique en los cartuchos las fechas en la cual la pasta fue creada. No compren bajo ninguna circunstancia una pasta que tenga 1 mes o mas de edad y, debido a que como usuarios aficionados no consumimos mucha pasta de estaño, compren esta pasta en cartuchos de no más de 5ccm.
En este momento realizo el perfil de temperatura, he hecho varios test, simplemente controlando la temperatura y regulando el horno manualmente. Apenas haya logrado realizar el circuito para medir las temperatura en el horno con un sensor PT1000 y el controlador mega8, haré un circuito que combine la medición de la temperatura y un relé con aislamiento óptico, para separar los circuitos digitales de la red eléctrica de 220VAC y controlar la función de calentamiento del horno para lograr de ese modo que el horno automáticamente ejecute el completo perfil como lo exige la hoja de datos con una precisión del tiempo y de la temperatura súper exacta. El tiempo obviamente en milisegundos, la temperatura con un error de menos de más o menor 0.5 Grados Celsius. La intención es conectar un Display gráfico y un codificador rotativo y teclas para poder programar los perfiles de forma manual o por interfaz directamente del ordenador.
Los detalles los publicaré tal cual avanzo.
Les quiero presentar otro reto que apareció en el curso del proyecto. La pregunta que lo hizo obvio es:
Como aplico la pasta de estaño a Pads, cuando quiero soldar un empaque con pines que tienen una distancia de centro de pin a centro de pin de solo 0.5 mm, y, si resuelvo esto, como pongo la componente en su sitio sin que la pasta de estaño, puesto en Pads tan pequeños y a tan pequeña distancia entre sí, sin embadurnar la pasta de estaño y crear cortos entro los pines. Piensen en un controlador ARM STM 32 Cortex, que viene en un LQFP100, con cíen pines todos a una distancia de 0.5 m de pin a pin. Aún peor, como quieren soldar un empaque como un LGA, donde el 90% de los pines y Pad no son accesibles ni visibles. Las componentes modernas, como por ejemplo fuentes de corriente constantes para LEDs con regulación de la intensidad de la luz y diagnostico para reconocer LEDs defectos, cortos y conexiones abiertas. He visto muestras de LGAs de 5x5 mm con distancias entre “pines” de o,6 mm!
Estoy en la fase de estudio para construir un equipo de precio muy moderado que permita realizar esto para aficionados a un precio de una fresa o torno. Los mantendré informados.