Construción Voilier según planos
- Hellmut1956
- Miembro Leal
- Mensajes: 1305
- Registrado: Sab Nov 29, 2008 2:06 pm
- Ubicación: Mammendorf, Alemania
Re: Construción Voilier según planos
Hola amigos
Finalmente he avanzado lo suficiente en los diversos temas relacionados con la electrónica que quería solucionar antes de continuar. Ahora quiero pedir ayuda. Quiero realizar el nombre del velero, Carina, en trabajo de marquetería creo que así se llama en Espanol. El casco recibirá un forro con chapa de madera caoba y en ese quiero integrar el nombre usando una madera de otro color. La letra que mas se aproxima a lo que busco es "Arial Rounded MT E", aunque no me gusta realmente aun. La letra la hare cursiva y "bold", y la "C" la hare más grande para poder poner las otras letras a media altura de la "C". Ojalá me explico.
Quizá alguno de ustedes tiene una sugerencia que puedo utilizar sin tener que pagar "copyright" u otros derechos de uso.
Recuerden que la letra debe poderse leer con facilidad desde cierta distancia y que tengo que realisarla tipo marquetería. Lo que quiero hacer es imprimir la letra en papel y pasarla a la madera de caoba para generar el "negativo" y luego en una madera de otro color realizar las letras en "positivo".
Una pregunta, quizá desplegando toda mi ignorancia en lo que a los verdaderos barcos concierne, pero el nombre de un barco se escribe solo a babor o también a estribor?
Finalmente he avanzado lo suficiente en los diversos temas relacionados con la electrónica que quería solucionar antes de continuar. Ahora quiero pedir ayuda. Quiero realizar el nombre del velero, Carina, en trabajo de marquetería creo que así se llama en Espanol. El casco recibirá un forro con chapa de madera caoba y en ese quiero integrar el nombre usando una madera de otro color. La letra que mas se aproxima a lo que busco es "Arial Rounded MT E", aunque no me gusta realmente aun. La letra la hare cursiva y "bold", y la "C" la hare más grande para poder poner las otras letras a media altura de la "C". Ojalá me explico.
Quizá alguno de ustedes tiene una sugerencia que puedo utilizar sin tener que pagar "copyright" u otros derechos de uso.
Recuerden que la letra debe poderse leer con facilidad desde cierta distancia y que tengo que realisarla tipo marquetería. Lo que quiero hacer es imprimir la letra en papel y pasarla a la madera de caoba para generar el "negativo" y luego en una madera de otro color realizar las letras en "positivo".
Una pregunta, quizá desplegando toda mi ignorancia en lo que a los verdaderos barcos concierne, pero el nombre de un barco se escribe solo a babor o también a estribor?
--------------------
Saludos Hellmut
Saludos Hellmut
- Joaquin Yarza
- Fundador
- Mensajes: 2636
- Registrado: Lun Ene 24, 2005 7:28 pm
Re: Construción Voilier según planos
Normalmente el nombre va en popa, en barcos deportivos los he visto con y sin nombre ni a babor ni a estribor, asi que no se lo que será obligatorio
- Hellmut1956
- Miembro Leal
- Mensajes: 1305
- Registrado: Sab Nov 29, 2008 2:06 pm
- Ubicación: Mammendorf, Alemania
Re: Construción Voilier según planos
Gracias Joaquin
Estuve investigando recientemente en unas revistas de veleros reales y es como tu dices. Aparentemente mi noción sobre este tema basa en el conocimiento de un novato en cosa de barcos y poco tiene que ver con la realidad. He decidido sin embargo escriber el nombre de "Carina" a ambos lados del casco adelante. Como creo ya haberlo narrado, el nombre sera realizado incrustando en la chapa de madera de caoba con la que forro el casco una chapa de una madera de color mas claro para que contraste con el color de la caoba. Ya pronto habra mas imagenes.
Un 2010 con salud, prosperidad y sin demasiados descontentos a todos
Hellmut
Estuve investigando recientemente en unas revistas de veleros reales y es como tu dices. Aparentemente mi noción sobre este tema basa en el conocimiento de un novato en cosa de barcos y poco tiene que ver con la realidad. He decidido sin embargo escriber el nombre de "Carina" a ambos lados del casco adelante. Como creo ya haberlo narrado, el nombre sera realizado incrustando en la chapa de madera de caoba con la que forro el casco una chapa de una madera de color mas claro para que contraste con el color de la caoba. Ya pronto habra mas imagenes.
Un 2010 con salud, prosperidad y sin demasiados descontentos a todos
Hellmut
--------------------
Saludos Hellmut
Saludos Hellmut
- Hellmut1956
- Miembro Leal
- Mensajes: 1305
- Registrado: Sab Nov 29, 2008 2:06 pm
- Ubicación: Mammendorf, Alemania
Re: Construción Voilier según planos
Hola amigos
Después de un prolongado tiempo sin actualizar el reporte me permito continuarlo. Hubo muy buenas razones, según mi opinión que me previnieron de continuar. La razón es que tenía que tomar decisiones que a su vez influyen otros aspectos de la construcción. Un tipo de problema del tipo, que existió primero, la gallina o el huevo! Prácticamente todos los temas los he tratado aquí en el foro en diversas partes según la rúbrica a la que corresponden. Este reporte de la construcción del velero tiene la intención de ser completo y poner todos los aspectos en relación.
Perdonen por lo tanto que tenga que narrar algunos temas y que en otros he tenido problemas en decidir cuál es el mejor orden en que presentarlos. Lo que reciben aquí es el resultado de presentarlo de la mejor forma posible, pero con la extensividad, error que peco siempre.
Prácticamente lo que toca hacer como próximo paso en la construcción del velero es completar la cubierta forrándola con madera triplex de 0,8 mm de grosor y luego preparar todo para poner los listones de la cubierta.
Uno de los problemas que me incapacitan en hacer esto es el cableado para la iluminación indirecta de la cubierta, son 36 luces realizadas con LEDs amarillas y cuya intensidad puede ser controlada desde el transmisor de mi radio control F14 Navy. Según para cual solución me decido el cableado varía substancialmente. Después de forrar la cubierta con una chapa de Triplex ya no me será posible acceder a aquellos puntos donde instalo el cableado.
Otro problema que tengo es que deseo fijar el listón que protege el casco de la fricción con el muelle. No conozco el término en español, Ustedes me lo dirán cuando os muestre fotos. Para que el reporte se más agradable de leer, aquí unas fotos:
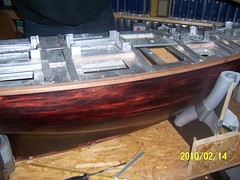
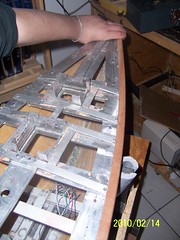
También este listón que bordea todo el casco siguiendo el borde de la cubierta representa varios retos. El uno es, como el cableado de las luces de la cubierta repercute. Ya que existe la posibilidad de poner el cableado dentro de este listón. Ya verán imágenes de su perfil.
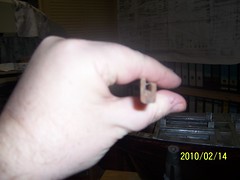
El otro es que debe pegarse exactamente a la superficie del casco y esto solo será posible cuando este haya sido forrado con la chapa de madera de caoba y esta haya sido laminada con fibra de vidrio y epoxi. Otro gran reto es de lograr en un 100% la simetría de la cubierta que se define por el trazado de este listón. Como todos ustedes saben, el ojo humano y la mente son los mejores instrumentos para detectar asimetrías.
Finalmente tengo que completar el espejo del casco de tal forma que este y el listón de protección de la cubierta cuadren de tal forma que al poner la cubierta sobre el casco la cubierta con su listón tenga la forma exacta del espejo. Pero el espejo también lo tengo que realizar de tal forma que pueda poner un primer “listón” de 1 cm de ancho de la chapa de caoba con la que forro el casco.
Y finalmente tengo que usar ese primer listón del forro del casco para lograr que la superficie del casco sobre la cual resta la cubierta desmontable se pegue perfectamente a la cubierta de aluminio para así garantizar una presión idéntica a lo largo de toda la línea de contacto entre la cubierta y el casco para lograr que el agua no pueda penetrar al casco.
Empecemos con el tema de la iluminación de la cubierta. Para referencia aquí 1 imagen con dos dibujos técnicos de las luces.
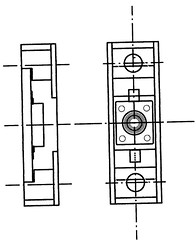
Estos dibujos muestran una vista lateral y una de arriba de cada luz, de las que voy a hacer unas 50. En el centro en la vista de arriba pueden ver la imagen del LED de primera generación con sus 2 pines, uno arriba, uno abajo. A los fines arriba y abajo ven un bloque que es de latón con una perforación de 3mm de diámetro para los tornillos sin cabeza, no sé cómo se llaman en Español. Allí se introducirán sendos tornillos de latón para atornillar la luz en la caja en la que se montará y atraves de las cuales se aplica la alimentación eléctrica al LED. En la vista de arriba pueden ver que todo esto viene empacado con chapas. En la vista lateral pueden ver el LED montado en la placa de 19x7 mm, aquí una imagen de esta:
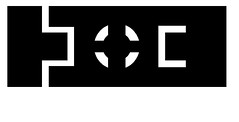
El LED necesita conectarse a una tensión de 2,7 V, por eso el Pad para soldar el pin a la izquierda está aislado eléctricamente del resto. Debajo del cuerpo del LED existe una superficie metálica que tiene la misma polaridad, tierra, como el pin a la derecha. La “cruz” tiene la función de indicarme dónde poner el estaño para soldar esta superficie con la cubierta de cobre de la placa, lo mismo la “u” a la derecha para el pin derecho.
Cuando hice los primeros experimentos con una primera luz que me armé resulto que la intensidad del LED de primera generación, un LED de OSRAM que requiere entre 20 y 30 mA máximo d corriente y una tensión de no más de 2,1 V y es de color amarillo, era miserable. No se imagina el problema de conseguir un proveedor de LEDs amarillas en un empaque pequeño de alta intensidad. Finalmente encontré este proveedor de unos LEDs “high brightness”, también de OSRAM, que permiten aplicarles hasta 350 mA y una tensión de 2,7 V. El empaque es algo mas grande, tiene un ancho, no de de 3,7 mm como el LED de primera generación, sino de 6,8 mm! Además requiere 4 pines lo que resulta en una placa bastante más complicada. Pero también resultaron 3 problemas adicionales, que luego tuvieron otras ramificaciones!
El uno es el costo. Los LED de primera generación me costaron 200 por algo más de 7 Euros inclusive el transporte, estos nuevos LED cuestan cada uno 1,20 Euros! Bueno, eso significa ahorrar durante un tiempo más prolongado, que tuve disponible por tener que resolver tantos problemas.
El segundo problema es la potencia de estos LEDs! Los LEDs de primera generación requerían 0,04 Wh, estos casi 1 Wh, y eso multiplicado por 36, el número de luces que instalaré. Normalmente conectar un LED es una labor muy simple. Supongamos una alimentación con una tensión de 5V, calculamos el valor de la resistencia según la ley de Ohm para limitar la corriente a los 20 mA deseados. Resulta en 0,04 Wh de energía útil para la luz generada por el LED y otros 0,04 Wh para el calor que se genera en la resistencia. Ahora estos LEDs de segunda generación requieren un máximo de casi 1 Wh, y la resistencia que limita la corriente a los 350mA máximos para el LED generan otro 1 Wh de calor. Son 35 Wh de calefacción y 35 Wh para generar la luz deseada! Necesitaría un bote acompañante que cargara con las baterías para alimentar el velero! Otro problema, y ese fueron violentos, es que cada LED requiere disipar gran parte del 1 Wh en calor para que el LED no se sobrecaliente. Aquí la descripción de como hice las placas de la primera generación, las de la segunda se harán de igual forma pero con unos aspectos adicionales!
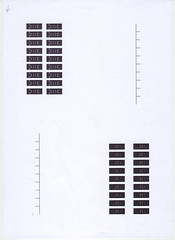
Aquí pueden ver una hoja de papel con 2 bloques de placas de las luces a 18 placas por bloque. Estos bloques los construí multiplicando la imagen de la placa que les mostré aquí más arriba usando el programa gratuito de CAD Solid Edge 2D Drafting. El bloque a la izquierda arriba tiene una geometría que permite un uso eficiente de la tarjeta foto sensitiva que utilicé. El próximo paso es cortar un pedazo del folio transparente para impresoras de tinta que cubra ese bloque y pegarlo por encima de la imagen en la hoja de papel. El resultado es que cuando imprimo la imagen una segunda vez, solo me gastaré una parte pequeña del folio transparente ahorrando así buena parte del costo considerable de los folios transparentes y logrando saber que la imagen será impresa en el folio de la forma que yo decida.
El próximo paso es revelar pasar la imagen del folio transparente a la placa foto sensitiva. Para este propósito me compré el bronceador de luz UV por eBay donde con paciencia se consigue por solo 1,- Euro debido a la gran oferta de estos aparatos. Aquí una imagen de un de estos bronceadores:

La próxima imagen muestra la construcción de mi máquina para transferir la imagen:
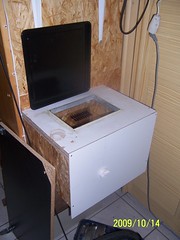
La tapa está abierta, en la superficie adelante se puede ver el control para el tiempo de iluminación del bronceador:
La próxima imagen muestre en detalle la superficie de vidrio con el folio con las imágenes de las placas y por debajo se ven los bombillos UV y el aparato bronceador. Lo monté de tal forma que las luces estuvieran paralelas a la superficie del vidrio y a una distancia de unos 10 cm para garantizar que la luz UV ilumine toda la superficie del vidrio con la misma intensidad. El borde de aluminio tiene 2 funciones. La uno es permitir colocar objetos en siempre el mismo lugar usando los bordes de aluminio como referencia, y la segunda función, aún más importante es garantizar que al poner la tapa esta no vaya a mover la placa foto sensitiva o el folio conduciendo la tapa con una superficie de espuma de goma en forma vertical. Aquí sigue la imagen de la máquina con la tapa puesta.
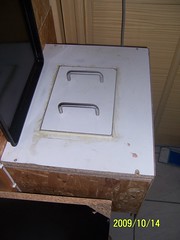
El uso de la máquina es de lo más simple. He puesto un interruptor en el cable de alimentación para poder desconectar la alimentación eléctrica en cualquier momento. Pongo el folio con la imagen impresa mirando hacia arriba para que la placa foto sensitiva reste directamente sobre la superficie con la imagen impresa y evitar que luz se difunda por debajo de la imagen. Después de poner la tapa alimento la máquina con electricidad activando el interruptor. Ahora giro el control del bronceador para que dure unos 30 minutos. Atraves de la ranura alrededor de la tapa puedo ver que la luz UV está encendida. Haciendo unos experimentos que he descrito en otro lugar en este foro, pude verificar que mi máquina requiere un tiempo de exposición de mínimo 6 minutos para pasar la imagen. A los 7 minutos uso el interruptor para desconectar la alimentación eléctrica y así apagar mi máquina bajo mi completo control.
Desafortunadamente no tome fotos de la tarjeta expuesta a la luz UV y después revelándola. Puse el líquido de revelación en un recipiente plano y después introduje la placa expuesta a la luz UV en el líquido y usé un pincel suave para ir moviendo el líquido sobre la superficie de la placa asegurando también que esta no flote evitando así la acción del líquido fe revelación. Después de muy corto tiempo se empieza a ver la imagen de las placas en un color verde claro y una estría de color negruzco se suelta de la superficie de la placa. Las placas de Bungartz que uso, son de calidad muy superiores a otras y perdonan un tiempo de revelación excesivo. Por eso es mejor dejar las placas un buen tiempo en el líquido de revelación. Una vez que ya no aparezca estrás por algún tiempo podemos suponer haber completado la revelación de la placa. Saco la placa y la lavo bajo agua corriente y limpia. Después la seco con una toalla vieja que tengo para este propósito. El líquido se puede guardar en una botella de plástico y yo he tenido buenos resultados con líquido de 1 año d edad!

La próxima imagen muestra que tan barato y simple es quitar la capa de cobre, aunque no dio que lo haya hecho de forma responsable. Tengo pensado construirme una máquina para este proceso. El reporte lo pondré a su debido tiempo. Uso una hornilla de gas de camping, un plato de vidrio de estos que resisten calor y otro pincel. El persulfato de sodio, un polvo blanco, se diluye en agua y se calienta a 40 grados centígrados. Como mi construcción es tan simple, voy revolviendo el ácido con el pincel para mantener el acido sobre la capa de cobre de la placa en movimiento. Así el líquido se calienta sobre la superficie del vidrio donde la llama lo calienta y después de cierto tiempo empiezan a crearse burbujas. Como revuelvo el líquido este se va calentando de forma pareja. Apenas tenga la impresión que ya está bastante caliente, apago la llama. El líquido reaccionando con el cobre crea burbujitas. Esto muestra la interacción. Moviendo e líquido con el pincel asegure que el acido sea reemplazado constantemente para evitar su saturación con cobre. Apenas tenga la impresión que el ácido se esté enfriando demasiado, vuelvo a encender el hornillo. Esto lo hago 2 a tres veces. Después de un cierto tiempo la capa de cobre empieza a oscurecerse y tomar el color verdoso del Epoxi de la placa. Con el pincel me dedico en especial a aquellas partes donde el cobre aún no haya sido eliminado. Una vez completado el proceso, saco la placa y la lavo con agua y luego la seco con una segunda toalla vieja que tengo para no contaminar las superficies.
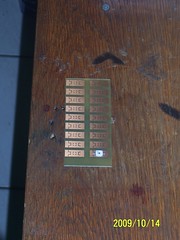
Aquí pueden ver la placa con las 18 placas para 18 luces. Puse un LED de primera generación en su lugar para mostrar las relaciones. Antes de seguir les quiero mostrar el horno que utilizo para soldar partes con empaques difíciles o pequeños como los LED o las componentes especiales que solo se consiguen en empaques muy pequeños.
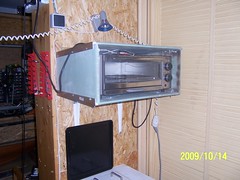
Aquí pueden ver el horno, un horno eléctrico para prepara pizzas que se consigue atraves del internet por muy poco dinero. El mío lo compré por Amazon por algo más de 50,- Euros por tener solo partes de acero inoxidable que no sufrirán por el calor al usarlo. La caja en la que lo monté es de un material aislante que no quema y es muy resistente al calor. A fin de cuentas no quiero que se me queme mi taller y mi casa!

La segunda imagen muestra en detalle el interior del horno y se ve el tubo que calienta el horno. Tiene el que se ve abajo, y uno igual arriba. Este horno me permite soldar componentes usando el sistema “reflow”. Este sistema requiere someter al estaño y a las partes a soldar a un perfil térmico que evitan que las componentes se dañen.
Después de un prolongado tiempo sin actualizar el reporte me permito continuarlo. Hubo muy buenas razones, según mi opinión que me previnieron de continuar. La razón es que tenía que tomar decisiones que a su vez influyen otros aspectos de la construcción. Un tipo de problema del tipo, que existió primero, la gallina o el huevo! Prácticamente todos los temas los he tratado aquí en el foro en diversas partes según la rúbrica a la que corresponden. Este reporte de la construcción del velero tiene la intención de ser completo y poner todos los aspectos en relación.
Perdonen por lo tanto que tenga que narrar algunos temas y que en otros he tenido problemas en decidir cuál es el mejor orden en que presentarlos. Lo que reciben aquí es el resultado de presentarlo de la mejor forma posible, pero con la extensividad, error que peco siempre.
Prácticamente lo que toca hacer como próximo paso en la construcción del velero es completar la cubierta forrándola con madera triplex de 0,8 mm de grosor y luego preparar todo para poner los listones de la cubierta.
Uno de los problemas que me incapacitan en hacer esto es el cableado para la iluminación indirecta de la cubierta, son 36 luces realizadas con LEDs amarillas y cuya intensidad puede ser controlada desde el transmisor de mi radio control F14 Navy. Según para cual solución me decido el cableado varía substancialmente. Después de forrar la cubierta con una chapa de Triplex ya no me será posible acceder a aquellos puntos donde instalo el cableado.
Otro problema que tengo es que deseo fijar el listón que protege el casco de la fricción con el muelle. No conozco el término en español, Ustedes me lo dirán cuando os muestre fotos. Para que el reporte se más agradable de leer, aquí unas fotos:
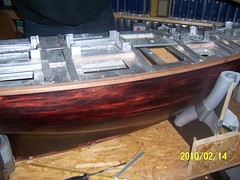
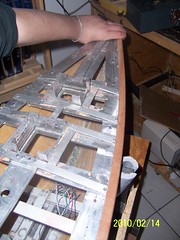
También este listón que bordea todo el casco siguiendo el borde de la cubierta representa varios retos. El uno es, como el cableado de las luces de la cubierta repercute. Ya que existe la posibilidad de poner el cableado dentro de este listón. Ya verán imágenes de su perfil.
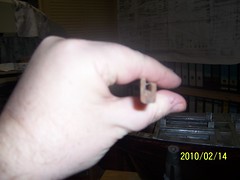
El otro es que debe pegarse exactamente a la superficie del casco y esto solo será posible cuando este haya sido forrado con la chapa de madera de caoba y esta haya sido laminada con fibra de vidrio y epoxi. Otro gran reto es de lograr en un 100% la simetría de la cubierta que se define por el trazado de este listón. Como todos ustedes saben, el ojo humano y la mente son los mejores instrumentos para detectar asimetrías.
Finalmente tengo que completar el espejo del casco de tal forma que este y el listón de protección de la cubierta cuadren de tal forma que al poner la cubierta sobre el casco la cubierta con su listón tenga la forma exacta del espejo. Pero el espejo también lo tengo que realizar de tal forma que pueda poner un primer “listón” de 1 cm de ancho de la chapa de caoba con la que forro el casco.
Y finalmente tengo que usar ese primer listón del forro del casco para lograr que la superficie del casco sobre la cual resta la cubierta desmontable se pegue perfectamente a la cubierta de aluminio para así garantizar una presión idéntica a lo largo de toda la línea de contacto entre la cubierta y el casco para lograr que el agua no pueda penetrar al casco.
Empecemos con el tema de la iluminación de la cubierta. Para referencia aquí 1 imagen con dos dibujos técnicos de las luces.
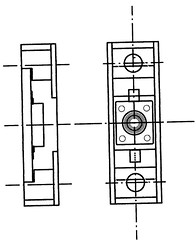
Estos dibujos muestran una vista lateral y una de arriba de cada luz, de las que voy a hacer unas 50. En el centro en la vista de arriba pueden ver la imagen del LED de primera generación con sus 2 pines, uno arriba, uno abajo. A los fines arriba y abajo ven un bloque que es de latón con una perforación de 3mm de diámetro para los tornillos sin cabeza, no sé cómo se llaman en Español. Allí se introducirán sendos tornillos de latón para atornillar la luz en la caja en la que se montará y atraves de las cuales se aplica la alimentación eléctrica al LED. En la vista de arriba pueden ver que todo esto viene empacado con chapas. En la vista lateral pueden ver el LED montado en la placa de 19x7 mm, aquí una imagen de esta:
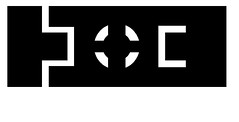
El LED necesita conectarse a una tensión de 2,7 V, por eso el Pad para soldar el pin a la izquierda está aislado eléctricamente del resto. Debajo del cuerpo del LED existe una superficie metálica que tiene la misma polaridad, tierra, como el pin a la derecha. La “cruz” tiene la función de indicarme dónde poner el estaño para soldar esta superficie con la cubierta de cobre de la placa, lo mismo la “u” a la derecha para el pin derecho.
Cuando hice los primeros experimentos con una primera luz que me armé resulto que la intensidad del LED de primera generación, un LED de OSRAM que requiere entre 20 y 30 mA máximo d corriente y una tensión de no más de 2,1 V y es de color amarillo, era miserable. No se imagina el problema de conseguir un proveedor de LEDs amarillas en un empaque pequeño de alta intensidad. Finalmente encontré este proveedor de unos LEDs “high brightness”, también de OSRAM, que permiten aplicarles hasta 350 mA y una tensión de 2,7 V. El empaque es algo mas grande, tiene un ancho, no de de 3,7 mm como el LED de primera generación, sino de 6,8 mm! Además requiere 4 pines lo que resulta en una placa bastante más complicada. Pero también resultaron 3 problemas adicionales, que luego tuvieron otras ramificaciones!
El uno es el costo. Los LED de primera generación me costaron 200 por algo más de 7 Euros inclusive el transporte, estos nuevos LED cuestan cada uno 1,20 Euros! Bueno, eso significa ahorrar durante un tiempo más prolongado, que tuve disponible por tener que resolver tantos problemas.
El segundo problema es la potencia de estos LEDs! Los LEDs de primera generación requerían 0,04 Wh, estos casi 1 Wh, y eso multiplicado por 36, el número de luces que instalaré. Normalmente conectar un LED es una labor muy simple. Supongamos una alimentación con una tensión de 5V, calculamos el valor de la resistencia según la ley de Ohm para limitar la corriente a los 20 mA deseados. Resulta en 0,04 Wh de energía útil para la luz generada por el LED y otros 0,04 Wh para el calor que se genera en la resistencia. Ahora estos LEDs de segunda generación requieren un máximo de casi 1 Wh, y la resistencia que limita la corriente a los 350mA máximos para el LED generan otro 1 Wh de calor. Son 35 Wh de calefacción y 35 Wh para generar la luz deseada! Necesitaría un bote acompañante que cargara con las baterías para alimentar el velero! Otro problema, y ese fueron violentos, es que cada LED requiere disipar gran parte del 1 Wh en calor para que el LED no se sobrecaliente. Aquí la descripción de como hice las placas de la primera generación, las de la segunda se harán de igual forma pero con unos aspectos adicionales!
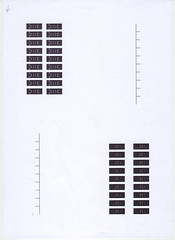
Aquí pueden ver una hoja de papel con 2 bloques de placas de las luces a 18 placas por bloque. Estos bloques los construí multiplicando la imagen de la placa que les mostré aquí más arriba usando el programa gratuito de CAD Solid Edge 2D Drafting. El bloque a la izquierda arriba tiene una geometría que permite un uso eficiente de la tarjeta foto sensitiva que utilicé. El próximo paso es cortar un pedazo del folio transparente para impresoras de tinta que cubra ese bloque y pegarlo por encima de la imagen en la hoja de papel. El resultado es que cuando imprimo la imagen una segunda vez, solo me gastaré una parte pequeña del folio transparente ahorrando así buena parte del costo considerable de los folios transparentes y logrando saber que la imagen será impresa en el folio de la forma que yo decida.
El próximo paso es revelar pasar la imagen del folio transparente a la placa foto sensitiva. Para este propósito me compré el bronceador de luz UV por eBay donde con paciencia se consigue por solo 1,- Euro debido a la gran oferta de estos aparatos. Aquí una imagen de un de estos bronceadores:

La próxima imagen muestra la construcción de mi máquina para transferir la imagen:
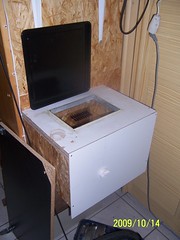
La tapa está abierta, en la superficie adelante se puede ver el control para el tiempo de iluminación del bronceador:
La próxima imagen muestre en detalle la superficie de vidrio con el folio con las imágenes de las placas y por debajo se ven los bombillos UV y el aparato bronceador. Lo monté de tal forma que las luces estuvieran paralelas a la superficie del vidrio y a una distancia de unos 10 cm para garantizar que la luz UV ilumine toda la superficie del vidrio con la misma intensidad. El borde de aluminio tiene 2 funciones. La uno es permitir colocar objetos en siempre el mismo lugar usando los bordes de aluminio como referencia, y la segunda función, aún más importante es garantizar que al poner la tapa esta no vaya a mover la placa foto sensitiva o el folio conduciendo la tapa con una superficie de espuma de goma en forma vertical. Aquí sigue la imagen de la máquina con la tapa puesta.
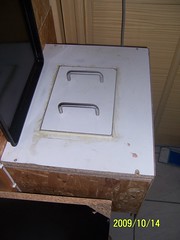
El uso de la máquina es de lo más simple. He puesto un interruptor en el cable de alimentación para poder desconectar la alimentación eléctrica en cualquier momento. Pongo el folio con la imagen impresa mirando hacia arriba para que la placa foto sensitiva reste directamente sobre la superficie con la imagen impresa y evitar que luz se difunda por debajo de la imagen. Después de poner la tapa alimento la máquina con electricidad activando el interruptor. Ahora giro el control del bronceador para que dure unos 30 minutos. Atraves de la ranura alrededor de la tapa puedo ver que la luz UV está encendida. Haciendo unos experimentos que he descrito en otro lugar en este foro, pude verificar que mi máquina requiere un tiempo de exposición de mínimo 6 minutos para pasar la imagen. A los 7 minutos uso el interruptor para desconectar la alimentación eléctrica y así apagar mi máquina bajo mi completo control.
Desafortunadamente no tome fotos de la tarjeta expuesta a la luz UV y después revelándola. Puse el líquido de revelación en un recipiente plano y después introduje la placa expuesta a la luz UV en el líquido y usé un pincel suave para ir moviendo el líquido sobre la superficie de la placa asegurando también que esta no flote evitando así la acción del líquido fe revelación. Después de muy corto tiempo se empieza a ver la imagen de las placas en un color verde claro y una estría de color negruzco se suelta de la superficie de la placa. Las placas de Bungartz que uso, son de calidad muy superiores a otras y perdonan un tiempo de revelación excesivo. Por eso es mejor dejar las placas un buen tiempo en el líquido de revelación. Una vez que ya no aparezca estrás por algún tiempo podemos suponer haber completado la revelación de la placa. Saco la placa y la lavo bajo agua corriente y limpia. Después la seco con una toalla vieja que tengo para este propósito. El líquido se puede guardar en una botella de plástico y yo he tenido buenos resultados con líquido de 1 año d edad!

La próxima imagen muestra que tan barato y simple es quitar la capa de cobre, aunque no dio que lo haya hecho de forma responsable. Tengo pensado construirme una máquina para este proceso. El reporte lo pondré a su debido tiempo. Uso una hornilla de gas de camping, un plato de vidrio de estos que resisten calor y otro pincel. El persulfato de sodio, un polvo blanco, se diluye en agua y se calienta a 40 grados centígrados. Como mi construcción es tan simple, voy revolviendo el ácido con el pincel para mantener el acido sobre la capa de cobre de la placa en movimiento. Así el líquido se calienta sobre la superficie del vidrio donde la llama lo calienta y después de cierto tiempo empiezan a crearse burbujas. Como revuelvo el líquido este se va calentando de forma pareja. Apenas tenga la impresión que ya está bastante caliente, apago la llama. El líquido reaccionando con el cobre crea burbujitas. Esto muestra la interacción. Moviendo e líquido con el pincel asegure que el acido sea reemplazado constantemente para evitar su saturación con cobre. Apenas tenga la impresión que el ácido se esté enfriando demasiado, vuelvo a encender el hornillo. Esto lo hago 2 a tres veces. Después de un cierto tiempo la capa de cobre empieza a oscurecerse y tomar el color verdoso del Epoxi de la placa. Con el pincel me dedico en especial a aquellas partes donde el cobre aún no haya sido eliminado. Una vez completado el proceso, saco la placa y la lavo con agua y luego la seco con una segunda toalla vieja que tengo para no contaminar las superficies.
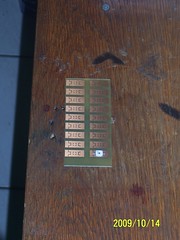
Aquí pueden ver la placa con las 18 placas para 18 luces. Puse un LED de primera generación en su lugar para mostrar las relaciones. Antes de seguir les quiero mostrar el horno que utilizo para soldar partes con empaques difíciles o pequeños como los LED o las componentes especiales que solo se consiguen en empaques muy pequeños.
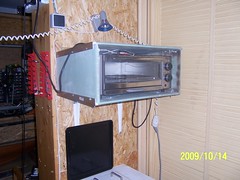
Aquí pueden ver el horno, un horno eléctrico para prepara pizzas que se consigue atraves del internet por muy poco dinero. El mío lo compré por Amazon por algo más de 50,- Euros por tener solo partes de acero inoxidable que no sufrirán por el calor al usarlo. La caja en la que lo monté es de un material aislante que no quema y es muy resistente al calor. A fin de cuentas no quiero que se me queme mi taller y mi casa!

La segunda imagen muestra en detalle el interior del horno y se ve el tubo que calienta el horno. Tiene el que se ve abajo, y uno igual arriba. Este horno me permite soldar componentes usando el sistema “reflow”. Este sistema requiere someter al estaño y a las partes a soldar a un perfil térmico que evitan que las componentes se dañen.
--------------------
Saludos Hellmut
Saludos Hellmut
- AXEL_WELLER
- Incondicional
- Mensajes: 750
- Registrado: Mié Jul 26, 2006 4:35 am
- Ubicación: Buenos Aires, Argentina
Re: Construción Voilier según planos
Saludos Hellmut, muy buen trabajo, muy explicado y completo, un trabajo aleman diria yo.
No comento nada ni pregunto pero sigo siempre tu hilo, espero ver avances mas seguidos.
Saludos.
No comento nada ni pregunto pero sigo siempre tu hilo, espero ver avances mas seguidos.
Saludos.
Buenos Aires, Argentina
en constuccion acorazado Graf Spee
http://www.modelismonaval.com/foro/view ... =21&t=4572" onclick="window.open(this.href);return false;
en constuccion acorazado Graf Spee
http://www.modelismonaval.com/foro/view ... =21&t=4572" onclick="window.open(this.href);return false;
- gerardo navarro
- VIP (Very Important Person)
- Mensajes: 6504
- Registrado: Sab Jun 06, 2009 2:11 pm
- Ubicación: Siempre en nuestro corazón
Re: Construción Voilier según planos
muy enteresante.......
saludos.......
saludos.......
EPD. En Memoria de Gerardo Navarro.
Un gran modelista y mejor persona.
Un gran modelista y mejor persona.
- Genaro Miranda
- Incondicional
- Mensajes: 896
- Registrado: Mar Feb 09, 2010 1:57 am
- Ubicación: Mexico,D.F.
- Contactar:
Re: Construción Voilier según planos

- Hellmut1956
- Miembro Leal
- Mensajes: 1305
- Registrado: Sab Nov 29, 2008 2:06 pm
- Ubicación: Mammendorf, Alemania
Re: Construción Voilier según planos
Bueno amigo
El velero progresa! Gracias al amigo "El Canario" (José)aquí en el foro hemos encontrado un camino que espero sea exitoso para poner el nombre del velero y su puerto de origen, "Guayaquil - Ecuador". Originalmente había planeado hacer lo con chapa de madera de 2 colores. La de caoba la utilizo para forrar todo el casco y una madera de color claro para incrustar las letras. Un amigo del foro aquí en Alemania me informo de algo que resulto en problemas que ahora, gracias a José, creo haber resuelto. El estilo de los primeros años del siglo 20 usaba una letra compleja, llena de adornos, esto cambió radicalmente con la aparición de la línea "bauhaus". Como mi velero es anterior a la época del bauhaus con sus formas geométricas, el realizar los textos incrustados resulta fuera de mis habilidades. José ahora me recomendó, combinando las informaciones que le había dado previamente de la hechura de las placas con ácido, donde el circuito es pasado a la placa por exposición con luz UV y luego revelado antes de poner lo en una solución de ácido, crear 2 placas de cada letra. Una, de latón de 0,2 mm, que será usada como letras y pegado al casco, y otra igual, llamada "neusilber" en alemán de 0,5 mm de grosor. El "neusilber es más duro que el latón. Lo que haré es usar la letras hechas con "neusilber" para incrustar una cavidad en la chapa de madera de caoba, 0,8 mm de grosor, poniendo la chapa de madera de caoba y la letras hechas en "neusilber" entre dos planchas de acero y presionar las en el tornillo de banco. En la cavidad creada así, fijada usando laca de poliuretano (G8 de Voss Chemie), introduzco la letra de latón de 0,2 mm de grosor.
Hoy me llegaron los serruchos para madera japoneses.
Aquí el enlace a la primera herramienta

Aquí el enlace a la segunda herramienta

La segunda herramienta tiene un perfil hecho expresamente para cortar madera en dirección vertical a la fibra de la maderas facilitando un corte limpio.
Las usaré para cortar las chapas de madera. Y también allí este amigo me ha dado una recomendación muy valiosa. Mi intención es forrar el casco usando tiras de la chapa de madera de caoba de 1 cm de ancho para dar la impresión que fueron usados listones de madera. Mis primeros intentos de lograr cortar estos listones de madera resultaron en mi incapacidad de cortar la chapa en franjas de igual ancho a todo su largo. Como resultado me esperaba tener que resolver el problema de cómo lograr que las ranuras debido al corte no estrictamente paralelo pudieran ser ocultadas. Gracias a los serruchos japoneses y a una tabla de madera que aquí llaman “mdf”, que no tiene estructuras por la fibra y que es muy lisa y de una superficie muy dura mis habilidades van a aumentar. Pero la idea de este amigo, que debido a los serruchos mencionados arriba, la cuchilla tiene un grosor de 0,3 mm, hacer los cortos oblicuos de tal forma que esto contrarreste irregularidades del corte. Imagínense que tan afilados son las cuchillas de estas herramientas japonesas, que resulta posible cortar una chapa de madera de forma oblicua!
El velero progresa! Gracias al amigo "El Canario" (José)aquí en el foro hemos encontrado un camino que espero sea exitoso para poner el nombre del velero y su puerto de origen, "Guayaquil - Ecuador". Originalmente había planeado hacer lo con chapa de madera de 2 colores. La de caoba la utilizo para forrar todo el casco y una madera de color claro para incrustar las letras. Un amigo del foro aquí en Alemania me informo de algo que resulto en problemas que ahora, gracias a José, creo haber resuelto. El estilo de los primeros años del siglo 20 usaba una letra compleja, llena de adornos, esto cambió radicalmente con la aparición de la línea "bauhaus". Como mi velero es anterior a la época del bauhaus con sus formas geométricas, el realizar los textos incrustados resulta fuera de mis habilidades. José ahora me recomendó, combinando las informaciones que le había dado previamente de la hechura de las placas con ácido, donde el circuito es pasado a la placa por exposición con luz UV y luego revelado antes de poner lo en una solución de ácido, crear 2 placas de cada letra. Una, de latón de 0,2 mm, que será usada como letras y pegado al casco, y otra igual, llamada "neusilber" en alemán de 0,5 mm de grosor. El "neusilber es más duro que el latón. Lo que haré es usar la letras hechas con "neusilber" para incrustar una cavidad en la chapa de madera de caoba, 0,8 mm de grosor, poniendo la chapa de madera de caoba y la letras hechas en "neusilber" entre dos planchas de acero y presionar las en el tornillo de banco. En la cavidad creada así, fijada usando laca de poliuretano (G8 de Voss Chemie), introduzco la letra de latón de 0,2 mm de grosor.
Hoy me llegaron los serruchos para madera japoneses.
Aquí el enlace a la primera herramienta

Aquí el enlace a la segunda herramienta

La segunda herramienta tiene un perfil hecho expresamente para cortar madera en dirección vertical a la fibra de la maderas facilitando un corte limpio.
Las usaré para cortar las chapas de madera. Y también allí este amigo me ha dado una recomendación muy valiosa. Mi intención es forrar el casco usando tiras de la chapa de madera de caoba de 1 cm de ancho para dar la impresión que fueron usados listones de madera. Mis primeros intentos de lograr cortar estos listones de madera resultaron en mi incapacidad de cortar la chapa en franjas de igual ancho a todo su largo. Como resultado me esperaba tener que resolver el problema de cómo lograr que las ranuras debido al corte no estrictamente paralelo pudieran ser ocultadas. Gracias a los serruchos japoneses y a una tabla de madera que aquí llaman “mdf”, que no tiene estructuras por la fibra y que es muy lisa y de una superficie muy dura mis habilidades van a aumentar. Pero la idea de este amigo, que debido a los serruchos mencionados arriba, la cuchilla tiene un grosor de 0,3 mm, hacer los cortos oblicuos de tal forma que esto contrarreste irregularidades del corte. Imagínense que tan afilados son las cuchillas de estas herramientas japonesas, que resulta posible cortar una chapa de madera de forma oblicua!
--------------------
Saludos Hellmut
Saludos Hellmut
Re: Construción Voilier según planos
Hola Hellmut, que tal estas? ya veo que estas "casi" en el final de tu construccion, perdona si no te he contestado antes pero es que no se por que razón en mi correo electronico se me habia almacenado como spam todas las ultimas publicaciones que han salido tuyas , y en eso que fui a ver ( por que mi hijo me lo vio y me lo dijo que tenia spam ) y veo las notificaciones al tema tuyo en ese apartado, las leí y ahora yaestoy al dia otra vez, tambien te diré que he comenzado mi proyecto de goleta de dos palos quiero ver si la adelanto y me pongo un dia en el foro y pongo las fotos por que no lo he hecho antes y tengo que enseñarme para poner fotos y comentarios , bueno un saludo y como siempre hay que quitarse el sombrero, como se dice aqui , por el trabajo que te estas tomando para hacer este fabuloso barco,animo.
- Hellmut1956
- Miembro Leal
- Mensajes: 1305
- Registrado: Sab Nov 29, 2008 2:06 pm
- Ubicación: Mammendorf, Alemania
Re: Construción Voilier según planos
Hola saoro
Bueno fuera si estuviera tan avanzado! Estoy avanzando pero el avanze es lento y dificultoso. Permitanme seguir contandoles la historia infinita del Carina!
Como pueden ver en la siguiente imagen los listones de madera de caoba aún no han sido tratadas:

Despues de aplicar laca de poliutherano 6 veces y de limar la superficie cada vez el resultado se pued eapreciar en las siguientes imagenes:
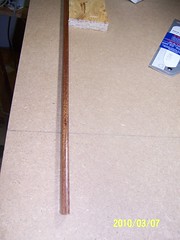
http://farm3.static.flickr.com/2733/441 ... 1314_m.jpg" onclick="window.open(this.href);return false;
Sigue una imagen donde se puede apreciar el primer corte que hice usando mis nuevas sierras japonesas mostradas antes:
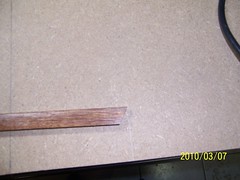
Como estos listones de madera de caoba tienen la función de protejer el casco de roces es necesario fijarlos fuertemente a los bordes de la cubierta completamente desmontable. Como lo he narrado antes, aluminio realmente no se deja pegar. Y pegar estos listones a la cubierta de aluminio es de mucha importancia. Esto me llevo a la siguiente idea para resolver el problema:

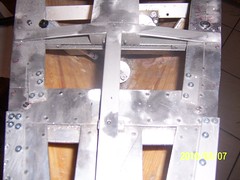
He empesado a atornillar a la estructura de aluminio listones de aluminio. En la primera imagen pueden ver los primeros 2 listones. El de la izquierda se ve atornillado y tiene pequenas perforaciones a lo largo del borde exterior. La contraparte a la derecha ya la puedo atornillar, pero aun no tiene las perforaciones! En la segunda imagen pueden ver un detalle del listón izquierdo, perdonen la mala calidad de la imagen. Aqui se ven muy claramente las pequenas perforaciones. La idea es usar el mismo pegante de epoxi para crear "remaches" que fijen el listón de madera al borde la cubierta. Como pueden ver en la próxima imagen:

el listón de madera tiene un perfil muy definido con 2 lenguas de diferente longitud. La más larga es aquella que estará situada arriba, la más corta se arrimará al casco asegurando así la línea correcta del listón. El aluminio de la cubierta, y en especial este listón adicional de aluminio encajará en la ranura. El epoxi que uso para pegar el liston de madera a la cubierta fluirá penetrando estas perforaciones uniendo así las superficies pegadas y el epoxi a ambos lados del aluminio creando así un remache que une el pegante epoxi. Esto evitará que el listón se pueda soltar y aumentará la rigidez de la unión.
Pero el listón de aluminio que atornillo ahora, que, debe estar montado un 100% simétrico en la cubierta, pues va a definir la geometría de la cubierta, cumple otra función adicional muy importante. Se ha demostrado, que los listones de aluminio grandes que forman la cubierta de aluminio tienen la tendencia a girar en torno al eje longitudinal y perdiendo así su función de garantizar una presión igual a lo largo de toda la superficie de contacto entre el casco y la cubierta, donde se encuentra la cinta aislante que evita que agua pueda penetrar al casco.
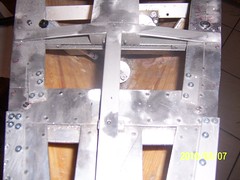
Como pueden apreciar en detalle en la próxima imagen había empesado a experimentar usando pequenas chapas de aluminio atornilladas en la uniones entre las bandas de aluminio longitudinales y las trasversales. Esas 2 chapas, una a la izquierda y una a la derecha fijan la posicion de los listones longitudinales evitando que estas puedan girar en torno al eje longitudinal. Ahora los listomes puestos para fijar el listón de madera tomará la función de las chapas. Esto se pued ever muy claramente en esta última imagen, donde 4 tornillitos avellanados aaseguran la unión rígida. Son estos numerosos detalles, resultado del analisis continuo, que demorán el progreso del velero.
Bueno fuera si estuviera tan avanzado! Estoy avanzando pero el avanze es lento y dificultoso. Permitanme seguir contandoles la historia infinita del Carina!
Como pueden ver en la siguiente imagen los listones de madera de caoba aún no han sido tratadas:

Despues de aplicar laca de poliutherano 6 veces y de limar la superficie cada vez el resultado se pued eapreciar en las siguientes imagenes:
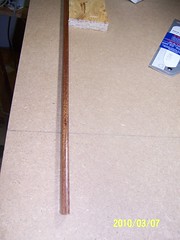
http://farm3.static.flickr.com/2733/441 ... 1314_m.jpg" onclick="window.open(this.href);return false;
Sigue una imagen donde se puede apreciar el primer corte que hice usando mis nuevas sierras japonesas mostradas antes:
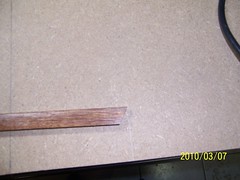
Como estos listones de madera de caoba tienen la función de protejer el casco de roces es necesario fijarlos fuertemente a los bordes de la cubierta completamente desmontable. Como lo he narrado antes, aluminio realmente no se deja pegar. Y pegar estos listones a la cubierta de aluminio es de mucha importancia. Esto me llevo a la siguiente idea para resolver el problema:

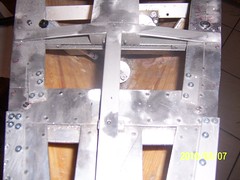
He empesado a atornillar a la estructura de aluminio listones de aluminio. En la primera imagen pueden ver los primeros 2 listones. El de la izquierda se ve atornillado y tiene pequenas perforaciones a lo largo del borde exterior. La contraparte a la derecha ya la puedo atornillar, pero aun no tiene las perforaciones! En la segunda imagen pueden ver un detalle del listón izquierdo, perdonen la mala calidad de la imagen. Aqui se ven muy claramente las pequenas perforaciones. La idea es usar el mismo pegante de epoxi para crear "remaches" que fijen el listón de madera al borde la cubierta. Como pueden ver en la próxima imagen:

el listón de madera tiene un perfil muy definido con 2 lenguas de diferente longitud. La más larga es aquella que estará situada arriba, la más corta se arrimará al casco asegurando así la línea correcta del listón. El aluminio de la cubierta, y en especial este listón adicional de aluminio encajará en la ranura. El epoxi que uso para pegar el liston de madera a la cubierta fluirá penetrando estas perforaciones uniendo así las superficies pegadas y el epoxi a ambos lados del aluminio creando así un remache que une el pegante epoxi. Esto evitará que el listón se pueda soltar y aumentará la rigidez de la unión.
Pero el listón de aluminio que atornillo ahora, que, debe estar montado un 100% simétrico en la cubierta, pues va a definir la geometría de la cubierta, cumple otra función adicional muy importante. Se ha demostrado, que los listones de aluminio grandes que forman la cubierta de aluminio tienen la tendencia a girar en torno al eje longitudinal y perdiendo así su función de garantizar una presión igual a lo largo de toda la superficie de contacto entre el casco y la cubierta, donde se encuentra la cinta aislante que evita que agua pueda penetrar al casco.
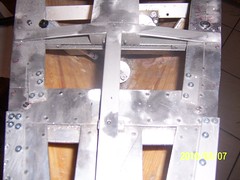
Como pueden apreciar en detalle en la próxima imagen había empesado a experimentar usando pequenas chapas de aluminio atornilladas en la uniones entre las bandas de aluminio longitudinales y las trasversales. Esas 2 chapas, una a la izquierda y una a la derecha fijan la posicion de los listones longitudinales evitando que estas puedan girar en torno al eje longitudinal. Ahora los listomes puestos para fijar el listón de madera tomará la función de las chapas. Esto se pued ever muy claramente en esta última imagen, donde 4 tornillitos avellanados aaseguran la unión rígida. Son estos numerosos detalles, resultado del analisis continuo, que demorán el progreso del velero.
--------------------
Saludos Hellmut
Saludos Hellmut
- Hellmut1956
- Miembro Leal
- Mensajes: 1305
- Registrado: Sab Nov 29, 2008 2:06 pm
- Ubicación: Mammendorf, Alemania
Re: Construción Voilier según planos
Como dije antes, muchos temas que tienen que ser resueltos antes de continuar me bloquearon e hicieron imposible avances visibles. El próximo punto, que creo ahora está resuelto, gracias al nuevo amigo aquí en Alemania y con el nombre de "El Canario" registrado en este foro, un Español de las Islas Canarias, tengo la solución.
Se trata del tema de cómo realizar poner el nombre del velero, "Carina" a ambos lados de la proa en el casco y como poner el puerto de origen, mi ciudad natal, Guayaquil, Ecuador en la popa.
Primero había elegido una letra de las que vienen con Windows. Entonces un amigo del foro aquí en Alemania trajo a mi atención, que el velero era de principio del siglo 20, pero antes de la aparición del estilo "bauhaus" con su afición por formas geométricas. En ese tiempo se estaba en la era del arte modernista con una afición por estilos barocos y exuberantes y que el uso de una letra barroca subrayaba el carácter de elite. Como estos veleros eran construidos para las personas más ricas de la época, que más digo, había que encontrar una letra nueva y más apropiada. Y a pesar de un estilo más baroco aún tenía que ser posible realizar el trabajo de incrustar las letras en el forro de chapa de madera de caoba. Pues bien, "El Canario", con una educación de albañil y de grafista pudo ayudarme en todos los frentes con sus excelentes conocimientos y su inventiva! El es mi profe en esta arena!
Permítanme poner estas 2 imágenes antes de continuar:
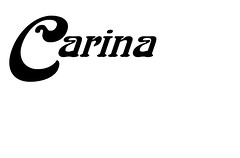
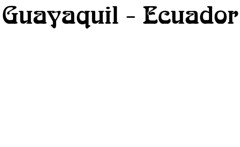
Pues bien, la letra usada es de 1905. En comparación con otras letras muchísimo más barrocas, está se podría realizar pero es, considerando el tamaño, un reto aún para un experto!
Pues bien, José, así se llama "El Canario", me hizo la propuesta de utilizar mi infraestructura y crear las letras siguiendo el mismo procedimiento que uso para crear placas electrónicas. Creo una película usando mi imprenta de tinta, expongo una chapa de latón a esta y luego la revelo y finalmente expongo la chapa al ácido. La chapa de latón tendrá un espesor de 0,2 mm. Repito el mismo procedimiento con otra chapa de un material más duro y de un grosor de 0,5 mm. Así tengo todas las letras requeridas 2 veces. Una vez de latón y que incrustaré en el forro de chapa de madera de caoba de 0,2 mm de grosor y una vez de este otro material con 0,5 mm de grosor. Ahora pongo la chapa de madera y las letras de un grosor de 0,5 mm entre dos placas de metal en forma de sándwich, y lo pongo en el tornillo de banco presionándolo lo más duro que pueda. El resultado será, que las letras serán incrustadas en la chapa de madera dejando una incrustación con una profundidad de mínimo esos 0,2 mm de profundidad y con la forma exactamente idéntica a las letras de latón.
Espero que en este proceso la chapa de madera va a deformarse un poco al ceder la madera y extenderse lateralmente. Esto lo corregiré inmediatamente con papel lija asegurando que los listones de chapa de madera no cambien su forma. Además pegaré la chapa de madera inmediatamente después de someterla a la presión en el tronillo de banco al casco. El Patex líquido aplicado, que debe secar por unos 10 minutos se pega al aplicarle una presión alta. Esto debería evitar posteriores deformaciones de la chapa de madera. Una vez completado el forrar del casco con la chapa de madera está será tratado con la laca de poliuretano de Voss Chemie, G8, que protege la madera endureciéndola y volviéndola resistente a la acción del agua. Espero que también tenga el efecto de fijar definitivamente la geometría de incrustación de las letras. Después de aplicar el número de capas de laca requeridas, mínimo unas 10 veces según mi experiencia y lijándolas cada vez, pego las letras de chapa de latón en su lugar esperando que así estas estén incrustadas de tal forma que sea posible lograr una superficie plana con la chapa de madera circundante.
Se trata del tema de cómo realizar poner el nombre del velero, "Carina" a ambos lados de la proa en el casco y como poner el puerto de origen, mi ciudad natal, Guayaquil, Ecuador en la popa.
Primero había elegido una letra de las que vienen con Windows. Entonces un amigo del foro aquí en Alemania trajo a mi atención, que el velero era de principio del siglo 20, pero antes de la aparición del estilo "bauhaus" con su afición por formas geométricas. En ese tiempo se estaba en la era del arte modernista con una afición por estilos barocos y exuberantes y que el uso de una letra barroca subrayaba el carácter de elite. Como estos veleros eran construidos para las personas más ricas de la época, que más digo, había que encontrar una letra nueva y más apropiada. Y a pesar de un estilo más baroco aún tenía que ser posible realizar el trabajo de incrustar las letras en el forro de chapa de madera de caoba. Pues bien, "El Canario", con una educación de albañil y de grafista pudo ayudarme en todos los frentes con sus excelentes conocimientos y su inventiva! El es mi profe en esta arena!
Permítanme poner estas 2 imágenes antes de continuar:
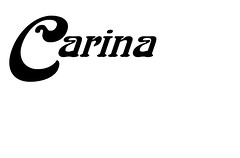
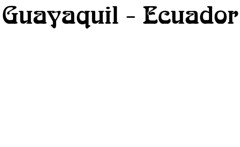
Pues bien, la letra usada es de 1905. En comparación con otras letras muchísimo más barrocas, está se podría realizar pero es, considerando el tamaño, un reto aún para un experto!
Pues bien, José, así se llama "El Canario", me hizo la propuesta de utilizar mi infraestructura y crear las letras siguiendo el mismo procedimiento que uso para crear placas electrónicas. Creo una película usando mi imprenta de tinta, expongo una chapa de latón a esta y luego la revelo y finalmente expongo la chapa al ácido. La chapa de latón tendrá un espesor de 0,2 mm. Repito el mismo procedimiento con otra chapa de un material más duro y de un grosor de 0,5 mm. Así tengo todas las letras requeridas 2 veces. Una vez de latón y que incrustaré en el forro de chapa de madera de caoba de 0,2 mm de grosor y una vez de este otro material con 0,5 mm de grosor. Ahora pongo la chapa de madera y las letras de un grosor de 0,5 mm entre dos placas de metal en forma de sándwich, y lo pongo en el tornillo de banco presionándolo lo más duro que pueda. El resultado será, que las letras serán incrustadas en la chapa de madera dejando una incrustación con una profundidad de mínimo esos 0,2 mm de profundidad y con la forma exactamente idéntica a las letras de latón.
Espero que en este proceso la chapa de madera va a deformarse un poco al ceder la madera y extenderse lateralmente. Esto lo corregiré inmediatamente con papel lija asegurando que los listones de chapa de madera no cambien su forma. Además pegaré la chapa de madera inmediatamente después de someterla a la presión en el tronillo de banco al casco. El Patex líquido aplicado, que debe secar por unos 10 minutos se pega al aplicarle una presión alta. Esto debería evitar posteriores deformaciones de la chapa de madera. Una vez completado el forrar del casco con la chapa de madera está será tratado con la laca de poliuretano de Voss Chemie, G8, que protege la madera endureciéndola y volviéndola resistente a la acción del agua. Espero que también tenga el efecto de fijar definitivamente la geometría de incrustación de las letras. Después de aplicar el número de capas de laca requeridas, mínimo unas 10 veces según mi experiencia y lijándolas cada vez, pego las letras de chapa de latón en su lugar esperando que así estas estén incrustadas de tal forma que sea posible lograr una superficie plana con la chapa de madera circundante.
--------------------
Saludos Hellmut
Saludos Hellmut
- gerardo navarro
- VIP (Very Important Person)
- Mensajes: 6504
- Registrado: Sab Jun 06, 2009 2:11 pm
- Ubicación: Siempre en nuestro corazón
Re: Construción Voilier según planos
me gustaron las letras, quedara muy bonito el nombre en ese estilo de letra, bacanas...........









EPD. En Memoria de Gerardo Navarro.
Un gran modelista y mejor persona.
Un gran modelista y mejor persona.
- Hellmut1956
- Miembro Leal
- Mensajes: 1305
- Registrado: Sab Nov 29, 2008 2:06 pm
- Ubicación: Mammendorf, Alemania
Re: Construción Voilier según planos
Hola amigos
Me llegaron las velas para el velero y hoy tuve la oportunidad de tomar una foto que qmuestra el casco del velero, el mastil y las velas. Ya pronto se verán progresoso sustanciosos!

Me llegaron las velas para el velero y hoy tuve la oportunidad de tomar una foto que qmuestra el casco del velero, el mastil y las velas. Ya pronto se verán progresoso sustanciosos!

--------------------
Saludos Hellmut
Saludos Hellmut
Re: Construción Voilier según planos
Hola Hellmut.
Estoy leyendo tu hilo, realmente impresionante,se nota que eres un perfeccionista.
Tengo una duda, con una estructura de aluminio tan conpleja aunque pese poco el aluminio no tienes miedo a subir excesivamente el centro de gravedad de la carena?.
Saludos ( con las velas se ve espectacular).
Estoy leyendo tu hilo, realmente impresionante,se nota que eres un perfeccionista.
Tengo una duda, con una estructura de aluminio tan conpleja aunque pese poco el aluminio no tienes miedo a subir excesivamente el centro de gravedad de la carena?.
Saludos ( con las velas se ve espectacular).
- Hellmut1956
- Miembro Leal
- Mensajes: 1305
- Registrado: Sab Nov 29, 2008 2:06 pm
- Ubicación: Mammendorf, Alemania
Re: Construción Voilier según planos
Hola Agripa
Gracias por tu amable comentario y tienes to´da la razón de preguntar como influye el centro de gravedad tán critico en veleros. Afortunadmente eso como todo es relativo. El velero va a pesar aprox. 21 kg, la estructura de aluminio pesa un poco más de 4 kg y se encuentra a solo 10 cm por encima de la superficie del agua, teniendo el casco un ancho de 32 cm. Eso significa que aunque considerable el peso de la cubierta creo que es tolerable. Confieso que no me he tomado el esfuerzo de reducir el peso de la estructura reduciendo la masa de aluminio creando huecos donde no afecta la estabilidad mecánica de la estructura. La razón tambien la confieso, y es que estoy ansioso de salir a manejarlo este verano.
Pero considerando la gran cantidad de plomo que tengo que poner en el fondo del casco para alcanzar el peso requerido, ls 5.5 kg de peso de las baterías!? Recuerdo que en algún punto escribi el peso del casco despues de soltarlo de la tabla en la cual lo construí, si no mal recuerdo, menos de 2 kg.
Gracias por tu amable comentario y tienes to´da la razón de preguntar como influye el centro de gravedad tán critico en veleros. Afortunadmente eso como todo es relativo. El velero va a pesar aprox. 21 kg, la estructura de aluminio pesa un poco más de 4 kg y se encuentra a solo 10 cm por encima de la superficie del agua, teniendo el casco un ancho de 32 cm. Eso significa que aunque considerable el peso de la cubierta creo que es tolerable. Confieso que no me he tomado el esfuerzo de reducir el peso de la estructura reduciendo la masa de aluminio creando huecos donde no afecta la estabilidad mecánica de la estructura. La razón tambien la confieso, y es que estoy ansioso de salir a manejarlo este verano.
Pero considerando la gran cantidad de plomo que tengo que poner en el fondo del casco para alcanzar el peso requerido, ls 5.5 kg de peso de las baterías!? Recuerdo que en algún punto escribi el peso del casco despues de soltarlo de la tabla en la cual lo construí, si no mal recuerdo, menos de 2 kg.
--------------------
Saludos Hellmut
Saludos Hellmut