Construción Voilier según planos
-
- Participativo
- Mensajes: 474
- Registrado: Vie Nov 30, 2007 4:32 pm
- Contactar:
Re: Construción Voilier según planos
Hola Hellmut
O produto tem muito interesse ; Ha´ ja´ algum tempo que gostaria de construir um veiculo rebocavel de transporte para os meus pequenos barcos , queria construi-lo leve ,mas para as soldaduras a aluminio era necessario o equipamento especial.
Esta ideia e´ boa , vou entrar em contacto para saber o preço das varetas .
Vai permitir construir um veiculo mais leve e seguro
Saludos
Carlos
O produto tem muito interesse ; Ha´ ja´ algum tempo que gostaria de construir um veiculo rebocavel de transporte para os meus pequenos barcos , queria construi-lo leve ,mas para as soldaduras a aluminio era necessario o equipamento especial.
Esta ideia e´ boa , vou entrar em contacto para saber o preço das varetas .
Vai permitir construir um veiculo mais leve e seguro
Saludos
Carlos
Portugal
Modelismo escala rc
http://www.facebook.com/antoniocarlos.mariano.16" onclick="window.open(this.href);return false;
Modelismo escala rc
http://www.facebook.com/antoniocarlos.mariano.16" onclick="window.open(this.href);return false;
- Hellmut1956
- Miembro Leal
- Mensajes: 1305
- Registrado: Sab Nov 29, 2008 2:06 pm
- Ubicación: Mammendorf, Alemania
Re: Construción Voilier según planos
Hola carlos, déjanos participar de tus experiencias con Durafix.
--------------------
Saludos Hellmut
Saludos Hellmut
Re: Construción Voilier según planos
Hola Hellmut soy saoro, no se si es por aqui por donde contactar contigo, hace algun tiempo que no escribes, yo he terminado mi barco y lo he publicado en construccion paso a paso, se llama goleta "Manuela" ya hablamos un saludo.
- Hellmut1956
- Miembro Leal
- Mensajes: 1305
- Registrado: Sab Nov 29, 2008 2:06 pm
- Ubicación: Mammendorf, Alemania
Re: Construción Voilier según planos
También aquí mi saludo saoro. He estado corto de medios económicos, lo que me ha tenido muy bloqueado por casi 2 meses. Afortunadamente finalmente han entrado primeros recursos que vuelven a creas una situación normal.
Efectivamente si he avanzado muchísimo con mi velero, pero son cosas que aún no se ven en el velero, pero estoy llegando al punto donde pondre la falsa cubierta en el velero. También he avanzado mucho con lo del receptáculo de las luces de cubierta, pero que da aún muy dificil por tener que encontrar una solución que permita el mantenimiento. El receptáculo tiene un sensor de temperatura y humedad y tengo que ver como lo hago, para poder cambiar el sensor sin romper cosas en la cubierta. Pero creo que en lo que queda del mes resolveré el problema. Ya he hecho algunas fotos, pero publicaré cuando tenga realizado el primer prototipo del receptáculo. Si voy a estar muy orgulloso pues he integrado muy diversas tecnologías en la realisación de esto. A ver cuando lo acabo.
Como he comentado he tenido éxitos soldando aluminio gracias al Duralfix recomendado aquí en el foro, ahora me falta herramientas para poder poner y fijar las partes mecanizadas en mi torno y soldarlas. Gracias a que ahora tengo los medios económicos pondre la orden por las herramientas el lunes. despues de soldarlas estoy finalmente, con ano de retraso, listo para poner la falsa cubierta. Eso es lo que no vi en el Manuela de saoro, el puso los listones sin falsa cibierta me pareció.
Logrado esto finalmente pondre el laminado con madera de caobo del casco y el nombre de "Carina" en latón. Tambien ahora gracias a la entrada de fondos puedo conseguir la placa para el BMS, Battery Monitoring System, sistema de monitoreo de baterías. esta placa tengo que reprogramarla, pues la consigo de mi proveedor del cargador Akkumatik, donde se utiliza com Balancer interno. Así que hasta bien entrada la primavera estoy colmado de trabajo y tengo lo que se requiere.
Efectivamente si he avanzado muchísimo con mi velero, pero son cosas que aún no se ven en el velero, pero estoy llegando al punto donde pondre la falsa cubierta en el velero. También he avanzado mucho con lo del receptáculo de las luces de cubierta, pero que da aún muy dificil por tener que encontrar una solución que permita el mantenimiento. El receptáculo tiene un sensor de temperatura y humedad y tengo que ver como lo hago, para poder cambiar el sensor sin romper cosas en la cubierta. Pero creo que en lo que queda del mes resolveré el problema. Ya he hecho algunas fotos, pero publicaré cuando tenga realizado el primer prototipo del receptáculo. Si voy a estar muy orgulloso pues he integrado muy diversas tecnologías en la realisación de esto. A ver cuando lo acabo.
Como he comentado he tenido éxitos soldando aluminio gracias al Duralfix recomendado aquí en el foro, ahora me falta herramientas para poder poner y fijar las partes mecanizadas en mi torno y soldarlas. Gracias a que ahora tengo los medios económicos pondre la orden por las herramientas el lunes. despues de soldarlas estoy finalmente, con ano de retraso, listo para poner la falsa cubierta. Eso es lo que no vi en el Manuela de saoro, el puso los listones sin falsa cibierta me pareció.
Logrado esto finalmente pondre el laminado con madera de caobo del casco y el nombre de "Carina" en latón. Tambien ahora gracias a la entrada de fondos puedo conseguir la placa para el BMS, Battery Monitoring System, sistema de monitoreo de baterías. esta placa tengo que reprogramarla, pues la consigo de mi proveedor del cargador Akkumatik, donde se utiliza com Balancer interno. Así que hasta bien entrada la primavera estoy colmado de trabajo y tengo lo que se requiere.
--------------------
Saludos Hellmut
Saludos Hellmut
Re: Construción Voilier según planos
Acabó de leer tu mensaje Hellmut y veo lo dificil que es el trabajo que estás haciendo, pues has metido en un barco de RC lo mismo casi que en un barco de verdad, carpinteria, diseño, claro, electricidad ,electronica, mecanica y lo mas importante el gusto por hacer las cosas ,bien hechas, muy muy bien hechas, animo que ya te queda menos,como dices yo no he hecho falsa cubierta directamente el liston sobre el bao, lo que he hecho es lo mismo que en modelismo estatico entre liston y liston, son de 3mm. espesorX 10mm. de ancho le he puesto otro liston de chapa de 1mm. de color cerezo, simulando asi el calafateado de las juntas, y bien pegado y luego con el barniz se hace todo un bloque que queda muy hermetico, bueno un saludo, ya hablamos.
- Hellmut1956
- Miembro Leal
- Mensajes: 1305
- Registrado: Sab Nov 29, 2008 2:06 pm
- Ubicación: Mammendorf, Alemania
Re: Construción Voilier según planos
Finalmente nuevas fotos de mis avances en la construcción del velero Carina! El propósito es mostrar el estado actual de los estudios y las realisaciones del receptáculo de las luces de iluminación indirecta de la cubierta, integrados en el barandal de mi velero (gracias a Genaro uso los términos mostrados en su hilo "PROYECTO DE REMOLCADOR DE PUERTO DE BILBAO").

Esta imagen muestra la forma de la placa que estoy disenando para el sensor de temperatura y de humedad completamente calibrado y que me da los valores medidos por el bus I2C de forma digital.
Para darles una noción de lo miniaturisado de esto, aquí una imagen del sensor:
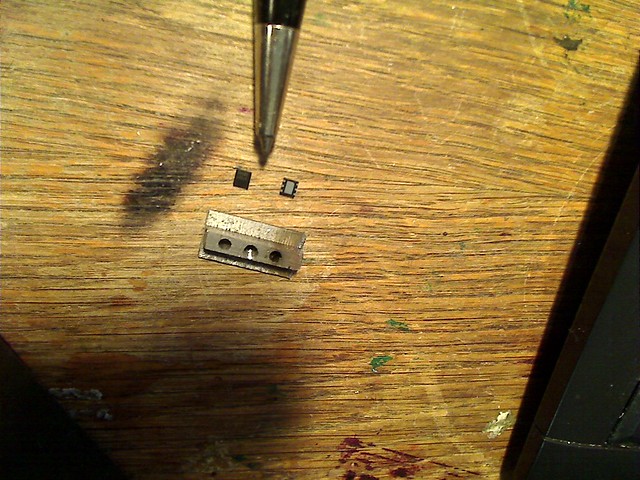
Pueden ver el empaque del sensor de 3x3mm con 6 pines junto a la punto de un bolígrafo. Asi se pueden imaginar que pequena es la placa y que finas las estructuras! La placa tiene una Forma de "T" invertida, la parte vertical es de 7x10mm, la ancha abajo es de 30x5mm. Los 2 pines centrales son las pistas de alimentación eléctrica de 3.0V del sensor, y como siempre con cada circuito integrado se requiere de un condensador de 100nF, este es de montaje de superficie en un empaque 0603, lo que refleja el tamano del empaque de 1.6x0.8mm, este se soldará en los 2 pads que se ven por encima de aquellos del sensor y que se monta entre Vcc y GND.
Como es requerimiento del bus I2C las 2 líneas, SCL, el tic del reloj (Clock) y SDA, la línea que transmite los datos en forma de bits, requieren de una resistencia "pull-up" o "jala-arriba", a VCC. Por eso, si se mira con lupa, se ven los pads de las dos pistas centrales y de la Vcc a la izquierda. Para la una uso una resistencia de 1k de un empaque 0805, o 2x1,25mm de tamano, es la segunda a la izquierda y Vcc la primera a la izquierda, donde se ve que las pista se vuelven algo mas anchas para formar el pad para esta resistencia.
Para la segunda resistencia tengo que realizar un puente de la tercera pista desde la izquierda a la primera a la izquierda por sobre la segunda. También aquí se puede ver un poco por debajo los pads. Para esto uso una resistencia en un empaque "mucho" mas grande, 1206, que tiene las dimensiones de 3.2x1.6mm. Como en la mitad el empaque no conduce polaridad puedo usarlo de puente!
En la parte horizontal de la placa ven 4 pads con un espacio sin el cobre de las pistas en el centro. Estos pads circulares tienen un radio de 2mm, los cables de latón de 0.5mm de diámetro serán soldados a estos pads e introducidos en la perforación de 0,8mm que haré en el centro. Esta parte de la placa es de 30x5mm.

Aquí ven una segunda versión de "estudio" de la placa del sensor. El objetivo es estudiar como puedo realizar el conjunto del receptáculo de las luces de cubierta de tal modo que en caso de necesidad pueda reemplazar la placa del sensor si el sensor se danara! Las dos barras horizontales de color verde con las paredes laterales de igual tamano de un perfil de latón de 10x10x1mm. 10mm de ancho, 10mm de alto de las paredes y 1mm de grosor del latón. Asi resulta un espacio interno de 8x9mm. Como pueden ver no es posible poner las componentes de la placa, el sensor, 3x3mm y el condensador y las 2 resistencias de tal forma en la placa que estas componentes se encuentren "dentro" del perfil de latón en forma de "U".
La parte horizontal de la placa de 30x5mm queda por debajo del perfil de latón. En esta versión de la placa, siendo modificada, aún pueden ver que no es posible pasar las 2 pistas interiores del sensor, SCL y SDA del bus I2C, a los pads circulares de 2mm de radio exteriores. Por eso estoy previendo 2 pads para "vias". Vias se llaman pistas electricas que van de una superficie de la placa a otra. Mi placa sera de 2 superficies, a ambos lados de la placa y los 2 pads pequenos de 1mm de radio son para pasar las pistas a la cara opuesta de la placa. En el lado opuesto habra 2 pads idénticos en la misma posición y 2 pads adicionales para volver la pista a la cara delantera de la placa, entre estos pads habra las pistas que los unen.
Adicionalmente pueden ver 2 bloques rectangulares verdes. Estos bloques son de la luz en el empaque. Me explico:

Aquí ven la placa de la que consiste la luz con la especialidad de tener un alma de aluminio y no de epoxi como acostumbran tener placas, de 3mm de grosor con el LED soldado en su posición. Es la primera placa "experimental" que construí para estudiar los problemas relacionados a este tipo de placas. Una historia en su propio derecho que aún no culminado. Con decirles que el proveedor no ha sido capaz aún de crear en buena calidad las pistas de cobre hasta el día de hoy (6 meses lleva este drama!), pero tengo suficientes usables para el propósito inicial.
Cada luz, aunque la construya en 10 anos, tiene que caber en cada receptáculo. Me construí un dispositivo donde armo las placas y las soldo a los bloques de latón, que en este momento aún son listones de 5x5mm de laton y que garantiza que las luces sean idénticas siempre:

Aquí pueden ver el dispositivo que consiste de 2 placas. Una de aluminio, que es aquella que utilizo para hacer las soldaduras en el horno de reflow, y una de epoxi, que uso para poder fijar las placas en su lugar de tal forma que tomen su posición correcta, donde aplico "soldering stop" una laca especial que limita las soldaduras a los pads y que previene que el estano fluya a donde no debe. Finalmente pude conseguir esto para mantenimiento y que se aplica con un pincel. Un gasto de casi 60,- Euros! Esto lo aplico en la placa y en los listones de latón para así evitar que el estano, aplicado como pasta antes de meter en el horno vaya a fluir a donde no debe y rendir la luz inoperable por corto circuitos. Pero también esto es un reporte propio en su propio derecho! Gracias al dispositivo de epoxi, al "soldering stop", a un pegante electricamente aislante pero que conduce calor, puedo fijar las placas en su lugar y medir que realmente no exista un corto ya antes de meter todo en el horno. Esto lo debo hacer placa por placa para evitar que los listones de latón falsifiquen las mediciones. Cuando las 18 placas han sido tratadas como descrito y el pegante y el soldering stop se hallan secado, pongo la placa de aluminio por encima. y paso por paso voy desatornillano todo y volverlo a atornillar ahora a la placa de aluminio! Entonces le aplico la pasta de estano "finepitch 6", una pasta de estano con las partículas sólidas mas diminutas en el mercado. Para esto uso unos cartuchos especiales que tengo que poner en agua de 50 grados centígrados para lograr una viscocidad tal que sea posible, con unas agujas especiales aplicar cantidades mínimas pero suficiente a los puntos a soldar. Siendo estos entre la cubierta de cobre de la plaquita para el LED y el LED, pero sin hacer un corto circuito con el alma de aluminio de las placas, y a la superficie central debajo del LED que sirve para transmitir el calor residual del LED a la placa y finalmente a los 2 pines del LED. Hecho esto pongo todo en el horno y someto el conjunto al perfil de calor exigido en la hoja de datos de las componetes para el proceso de reflow.
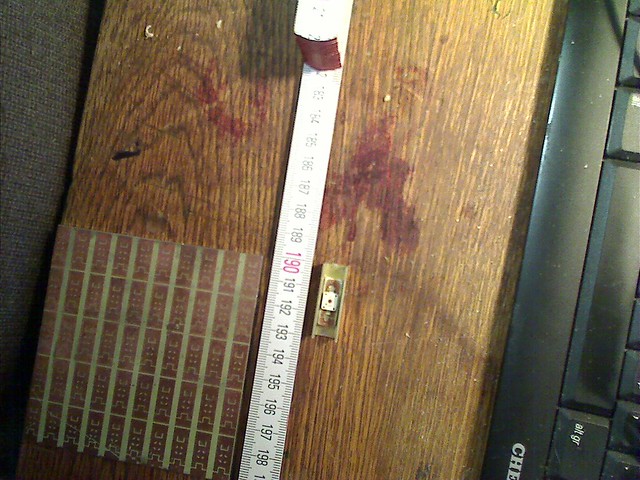
Aquí la imagen del listón de latón con perfil "U" y la plaquita con el LED tal cual la luz estara en el receptácula que forma el liston delatón en forma de "U".
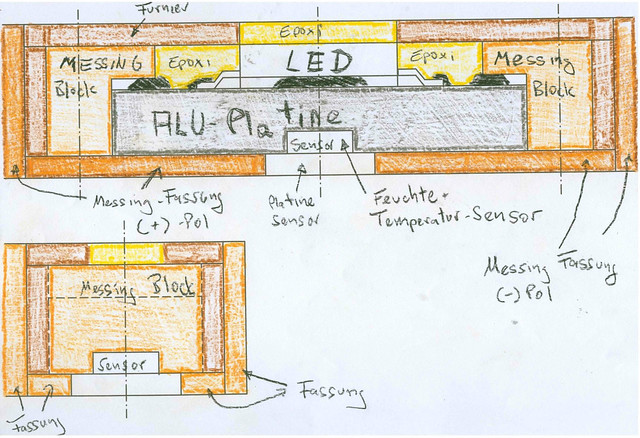
Aquí otro esquema de la luz de cubierta que junto con la imagen de la plaquita del LED ilustra de que hablo, ojalá!
Aquí pueden ver 2 vistas del recetáculo con la luz instalada. Este gráfico ya es algo mas antiguo, pues voy estudiando y entendiendo el conjunto y así decidiendo como hacerlo!
En la imagen superior pueden ver una vista lateral del receptáculo, es la estructura exterior de color anaranjado y que es equivalente al perfil "U" de latón que ven arriba con la placa del LED adentro. Los 2 bloques laterales anaranjados "Messing Block" son equivalentes a los 2 bloques verdes en el esquema de la placa del sensor arriba, y a los que soldo la placa con alma de aluminio, color gris en el dibujo. O sea los listones de latón que ven en el dispositivo para construir las luces. Tambien pueden ver la posición del sensor debajo del LED y de su placa en una ranura que freso por debajo a la plaquita del LED. Asi el LED, cuando se calienta, calienta el aluminio de la placa y esta calienta el aire en la ranura donde se encuentra el sensor! la electrónica se encarga de limitar la corriente que fluye atraves del LED a tales valores que la temperatura medidad por el sendor por ejemplo no sobrepase los 70-80 Grados celsius. Para esto uso una compoente muy sofisticada de Freeescale, el MC34844, que me permite generar hasta 60V desde los 24-39,6V que me brindan las baterías a bordo del velero permitiendo así poner un elevado número de LEDs en serie. Ademas el componente me permite controlar, para así controlar por radio control, la intensidad de la luz emitada por el LED. Hasta 10 canales a 50mA, cada canal en 256 pasos. Para mis LEDs de las luces de cubierta requiero hasta 400mA de corriente continua, por lo que tengo que conectar 8 canales en paralelo a los LEDs. esto me brinda la oportunidad de controlar laintensidad de las luces en 8x256 pasos o un total de 2048 pasos!
Para completar el reporte de hoy, aquí una imagen de un esquema que muestra como las luces de iluminación indirectas y sus receptáculos correspondientes estarán integrados en el barandal del velero:
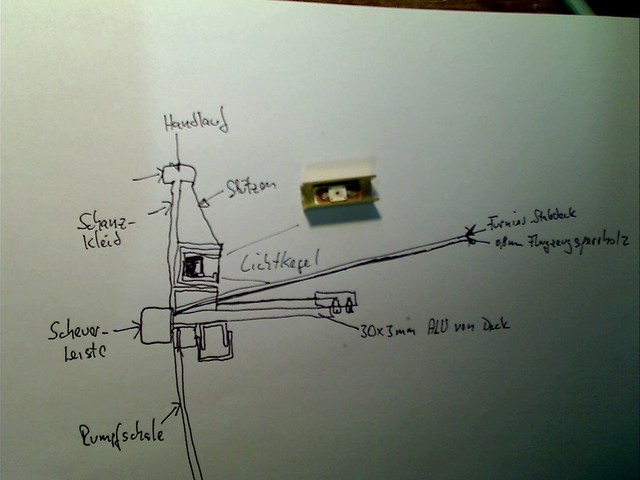
Sigue para referencia una imagen de la estructura de aluminio de la cubierta desmontable del velero:
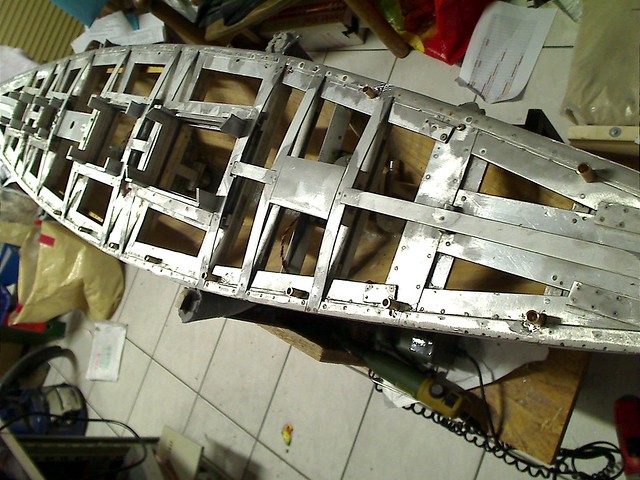
Como pueden ver en el esquema, el perfil "U" de latón va de tal forma que la parte abierta mira en dirección de la cubierta hacia el centro y en la horizontal. El perfil "U" viene montado en un pedestal de latón de 5x7mm de perfil rectangular, soldado a este usando pasta de estanp especial para latón. El conjunto de pedestal y perfil U forman el conjunto de receptáculo de las luces. En el pedestal freso unas ranura de 0.8mm de ancho para dar espacio a los cables de latón que vienen de la placa del sensor. Estos cables vienen aislados electricamente con un tubo térmoretractil y pasan por sendas ranuras. En total 4 para cada uno de las pistas que vienen del sensor. El calor residual orginado por el LED de la luz, hasta 400mA pueden generar muchísima energía térmica, pasa del LED al alma de aluminio de la placa del LED yesta, en contacto directo con el perfil U de latón del receptáculo,paso el calor al perfil U. De este el calor pasa al pedestal de laton y del pedestal de latón a la barrade 3x30mm de aluminio que pueden ver en la imagen de la cubierta de aluminio! Como se pueden imaginar este camino hace de la estructura de aluminio de la cuberta un potente y grandísimo difusor de calor para todos los LEDs en el velero! esto de por si, aún es bastante simple!
Yo tengo el objetivo de realizar el conjnto de receptáculo de tal forma, que si el sensor se fuera a danar sea posible reemplazar la placa del sensor con un sensor nuevo sin danar la cubierta. Por esta razón, el pedestal del receptáculo es unido a la barra de aluminio de la cubierta atornillandolo con tornillos sincabeza de latón. esto tiene un doble objetivo. Por un lado se logra fijar de forma sólida el conjunto de receptáculo en su posición integrada al barandal de la cubierta del velero, pero por estar solo atornillado esta unión puede ser desatornillada por abajo. Ahora, continuado entornillando el tornillo sin cabeza acaba empujando el conjunto de receptáculo hacia arriba, pues la rosca en su lado superior choca con el perfil U de laton soldado al pedestal y asi el tornillo, soprtado por el aluminio de la estructura de la cubierta empuja el conjunto hacia arriba! Por otro lado el conjunto en su lado posterior esta en contacto con la superficie de chapa de madera del barandal, que ha sido realizado de tal forma que permita que le conjunto de receptáculo se deslize en su movimiento hacia arriba. Las fisuras entre la pared interior del barandal y el conjunto del receptáculo son tapadas usando el espray de "Plastico" de Kontakt Chemie, un espray usado para impermeablizar circuitos electrónicos. este espray es aplicado a todas las fisuras entre el conjunto de receptáculo y su entorno, como también entrela luz y el receptáculo. Si esta impermeabilisación resultara danada, esto afectaría la humedad ambiental dentro del receptáculo y el sensor usado registraría un cambio de la humedad ambiental y así me daría reporte de revisar la impermeabilidad del conjunto de receptáculo y luz"! Se que es una locura, pero me parece genial. El sensor SHT21 se la empresa Sensirion, una nueva e inovativa empresa que resultó del ámbito de la prestigiosa universidad ETH Zurich, fuera de medir la temperatura, mide la humedad y da los datos completamente calibrados y de forma digital. No existen experiencias de un uso como el previsto, lo que hace de este velero lo mas avanzado en cuentión de electrónica!

Esta imagen muestra la forma de la placa que estoy disenando para el sensor de temperatura y de humedad completamente calibrado y que me da los valores medidos por el bus I2C de forma digital.
Para darles una noción de lo miniaturisado de esto, aquí una imagen del sensor:
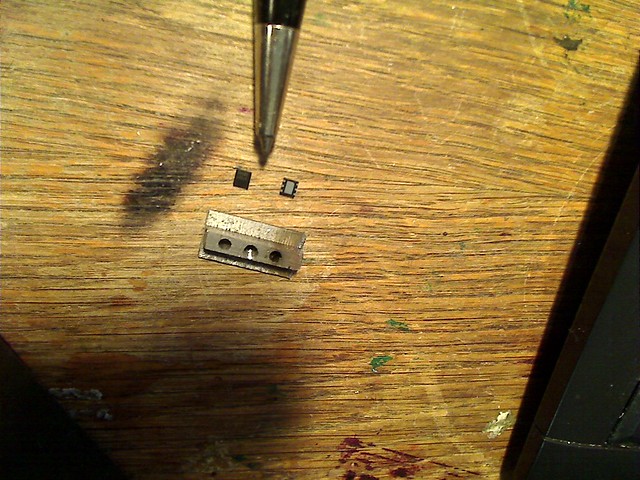
Pueden ver el empaque del sensor de 3x3mm con 6 pines junto a la punto de un bolígrafo. Asi se pueden imaginar que pequena es la placa y que finas las estructuras! La placa tiene una Forma de "T" invertida, la parte vertical es de 7x10mm, la ancha abajo es de 30x5mm. Los 2 pines centrales son las pistas de alimentación eléctrica de 3.0V del sensor, y como siempre con cada circuito integrado se requiere de un condensador de 100nF, este es de montaje de superficie en un empaque 0603, lo que refleja el tamano del empaque de 1.6x0.8mm, este se soldará en los 2 pads que se ven por encima de aquellos del sensor y que se monta entre Vcc y GND.
Como es requerimiento del bus I2C las 2 líneas, SCL, el tic del reloj (Clock) y SDA, la línea que transmite los datos en forma de bits, requieren de una resistencia "pull-up" o "jala-arriba", a VCC. Por eso, si se mira con lupa, se ven los pads de las dos pistas centrales y de la Vcc a la izquierda. Para la una uso una resistencia de 1k de un empaque 0805, o 2x1,25mm de tamano, es la segunda a la izquierda y Vcc la primera a la izquierda, donde se ve que las pista se vuelven algo mas anchas para formar el pad para esta resistencia.
Para la segunda resistencia tengo que realizar un puente de la tercera pista desde la izquierda a la primera a la izquierda por sobre la segunda. También aquí se puede ver un poco por debajo los pads. Para esto uso una resistencia en un empaque "mucho" mas grande, 1206, que tiene las dimensiones de 3.2x1.6mm. Como en la mitad el empaque no conduce polaridad puedo usarlo de puente!
En la parte horizontal de la placa ven 4 pads con un espacio sin el cobre de las pistas en el centro. Estos pads circulares tienen un radio de 2mm, los cables de latón de 0.5mm de diámetro serán soldados a estos pads e introducidos en la perforación de 0,8mm que haré en el centro. Esta parte de la placa es de 30x5mm.

Aquí ven una segunda versión de "estudio" de la placa del sensor. El objetivo es estudiar como puedo realizar el conjunto del receptáculo de las luces de cubierta de tal modo que en caso de necesidad pueda reemplazar la placa del sensor si el sensor se danara! Las dos barras horizontales de color verde con las paredes laterales de igual tamano de un perfil de latón de 10x10x1mm. 10mm de ancho, 10mm de alto de las paredes y 1mm de grosor del latón. Asi resulta un espacio interno de 8x9mm. Como pueden ver no es posible poner las componentes de la placa, el sensor, 3x3mm y el condensador y las 2 resistencias de tal forma en la placa que estas componentes se encuentren "dentro" del perfil de latón en forma de "U".
La parte horizontal de la placa de 30x5mm queda por debajo del perfil de latón. En esta versión de la placa, siendo modificada, aún pueden ver que no es posible pasar las 2 pistas interiores del sensor, SCL y SDA del bus I2C, a los pads circulares de 2mm de radio exteriores. Por eso estoy previendo 2 pads para "vias". Vias se llaman pistas electricas que van de una superficie de la placa a otra. Mi placa sera de 2 superficies, a ambos lados de la placa y los 2 pads pequenos de 1mm de radio son para pasar las pistas a la cara opuesta de la placa. En el lado opuesto habra 2 pads idénticos en la misma posición y 2 pads adicionales para volver la pista a la cara delantera de la placa, entre estos pads habra las pistas que los unen.
Adicionalmente pueden ver 2 bloques rectangulares verdes. Estos bloques son de la luz en el empaque. Me explico:

Aquí ven la placa de la que consiste la luz con la especialidad de tener un alma de aluminio y no de epoxi como acostumbran tener placas, de 3mm de grosor con el LED soldado en su posición. Es la primera placa "experimental" que construí para estudiar los problemas relacionados a este tipo de placas. Una historia en su propio derecho que aún no culminado. Con decirles que el proveedor no ha sido capaz aún de crear en buena calidad las pistas de cobre hasta el día de hoy (6 meses lleva este drama!), pero tengo suficientes usables para el propósito inicial.
Cada luz, aunque la construya en 10 anos, tiene que caber en cada receptáculo. Me construí un dispositivo donde armo las placas y las soldo a los bloques de latón, que en este momento aún son listones de 5x5mm de laton y que garantiza que las luces sean idénticas siempre:

Aquí pueden ver el dispositivo que consiste de 2 placas. Una de aluminio, que es aquella que utilizo para hacer las soldaduras en el horno de reflow, y una de epoxi, que uso para poder fijar las placas en su lugar de tal forma que tomen su posición correcta, donde aplico "soldering stop" una laca especial que limita las soldaduras a los pads y que previene que el estano fluya a donde no debe. Finalmente pude conseguir esto para mantenimiento y que se aplica con un pincel. Un gasto de casi 60,- Euros! Esto lo aplico en la placa y en los listones de latón para así evitar que el estano, aplicado como pasta antes de meter en el horno vaya a fluir a donde no debe y rendir la luz inoperable por corto circuitos. Pero también esto es un reporte propio en su propio derecho! Gracias al dispositivo de epoxi, al "soldering stop", a un pegante electricamente aislante pero que conduce calor, puedo fijar las placas en su lugar y medir que realmente no exista un corto ya antes de meter todo en el horno. Esto lo debo hacer placa por placa para evitar que los listones de latón falsifiquen las mediciones. Cuando las 18 placas han sido tratadas como descrito y el pegante y el soldering stop se hallan secado, pongo la placa de aluminio por encima. y paso por paso voy desatornillano todo y volverlo a atornillar ahora a la placa de aluminio! Entonces le aplico la pasta de estano "finepitch 6", una pasta de estano con las partículas sólidas mas diminutas en el mercado. Para esto uso unos cartuchos especiales que tengo que poner en agua de 50 grados centígrados para lograr una viscocidad tal que sea posible, con unas agujas especiales aplicar cantidades mínimas pero suficiente a los puntos a soldar. Siendo estos entre la cubierta de cobre de la plaquita para el LED y el LED, pero sin hacer un corto circuito con el alma de aluminio de las placas, y a la superficie central debajo del LED que sirve para transmitir el calor residual del LED a la placa y finalmente a los 2 pines del LED. Hecho esto pongo todo en el horno y someto el conjunto al perfil de calor exigido en la hoja de datos de las componetes para el proceso de reflow.
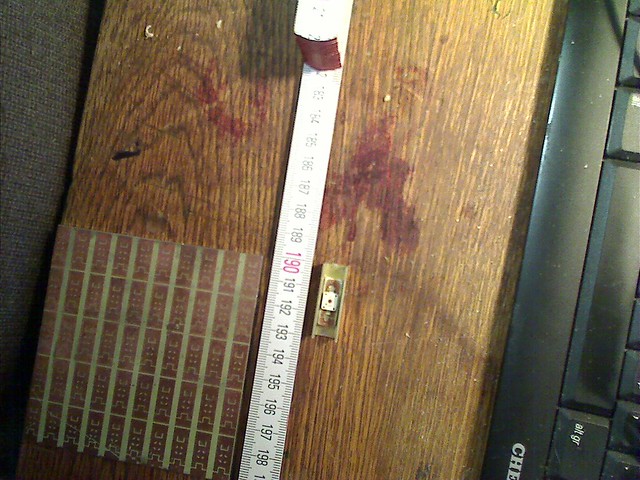
Aquí la imagen del listón de latón con perfil "U" y la plaquita con el LED tal cual la luz estara en el receptácula que forma el liston delatón en forma de "U".
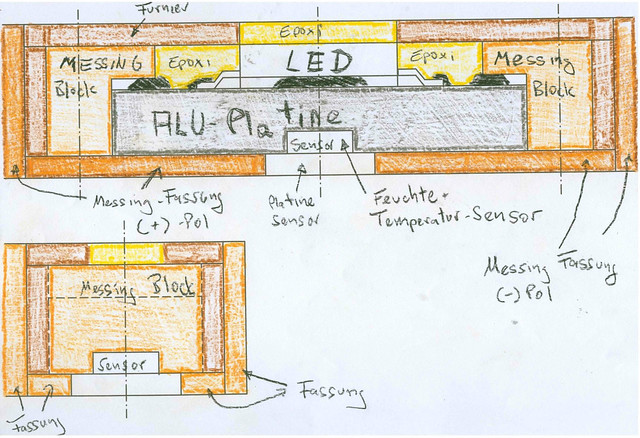
Aquí otro esquema de la luz de cubierta que junto con la imagen de la plaquita del LED ilustra de que hablo, ojalá!
Aquí pueden ver 2 vistas del recetáculo con la luz instalada. Este gráfico ya es algo mas antiguo, pues voy estudiando y entendiendo el conjunto y así decidiendo como hacerlo!
En la imagen superior pueden ver una vista lateral del receptáculo, es la estructura exterior de color anaranjado y que es equivalente al perfil "U" de latón que ven arriba con la placa del LED adentro. Los 2 bloques laterales anaranjados "Messing Block" son equivalentes a los 2 bloques verdes en el esquema de la placa del sensor arriba, y a los que soldo la placa con alma de aluminio, color gris en el dibujo. O sea los listones de latón que ven en el dispositivo para construir las luces. Tambien pueden ver la posición del sensor debajo del LED y de su placa en una ranura que freso por debajo a la plaquita del LED. Asi el LED, cuando se calienta, calienta el aluminio de la placa y esta calienta el aire en la ranura donde se encuentra el sensor! la electrónica se encarga de limitar la corriente que fluye atraves del LED a tales valores que la temperatura medidad por el sendor por ejemplo no sobrepase los 70-80 Grados celsius. Para esto uso una compoente muy sofisticada de Freeescale, el MC34844, que me permite generar hasta 60V desde los 24-39,6V que me brindan las baterías a bordo del velero permitiendo así poner un elevado número de LEDs en serie. Ademas el componente me permite controlar, para así controlar por radio control, la intensidad de la luz emitada por el LED. Hasta 10 canales a 50mA, cada canal en 256 pasos. Para mis LEDs de las luces de cubierta requiero hasta 400mA de corriente continua, por lo que tengo que conectar 8 canales en paralelo a los LEDs. esto me brinda la oportunidad de controlar laintensidad de las luces en 8x256 pasos o un total de 2048 pasos!
Para completar el reporte de hoy, aquí una imagen de un esquema que muestra como las luces de iluminación indirectas y sus receptáculos correspondientes estarán integrados en el barandal del velero:
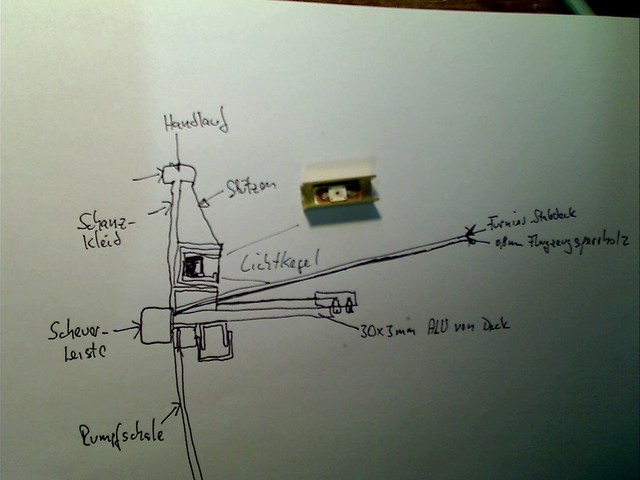
Sigue para referencia una imagen de la estructura de aluminio de la cubierta desmontable del velero:
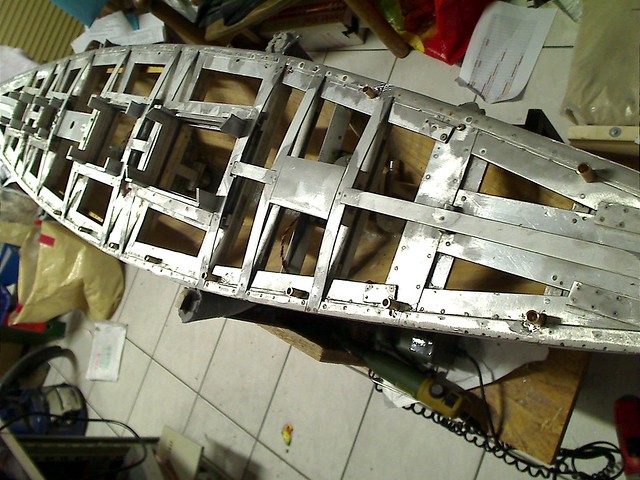
Como pueden ver en el esquema, el perfil "U" de latón va de tal forma que la parte abierta mira en dirección de la cubierta hacia el centro y en la horizontal. El perfil "U" viene montado en un pedestal de latón de 5x7mm de perfil rectangular, soldado a este usando pasta de estanp especial para latón. El conjunto de pedestal y perfil U forman el conjunto de receptáculo de las luces. En el pedestal freso unas ranura de 0.8mm de ancho para dar espacio a los cables de latón que vienen de la placa del sensor. Estos cables vienen aislados electricamente con un tubo térmoretractil y pasan por sendas ranuras. En total 4 para cada uno de las pistas que vienen del sensor. El calor residual orginado por el LED de la luz, hasta 400mA pueden generar muchísima energía térmica, pasa del LED al alma de aluminio de la placa del LED yesta, en contacto directo con el perfil U de latón del receptáculo,paso el calor al perfil U. De este el calor pasa al pedestal de laton y del pedestal de latón a la barrade 3x30mm de aluminio que pueden ver en la imagen de la cubierta de aluminio! Como se pueden imaginar este camino hace de la estructura de aluminio de la cuberta un potente y grandísimo difusor de calor para todos los LEDs en el velero! esto de por si, aún es bastante simple!
Yo tengo el objetivo de realizar el conjnto de receptáculo de tal forma, que si el sensor se fuera a danar sea posible reemplazar la placa del sensor con un sensor nuevo sin danar la cubierta. Por esta razón, el pedestal del receptáculo es unido a la barra de aluminio de la cubierta atornillandolo con tornillos sincabeza de latón. esto tiene un doble objetivo. Por un lado se logra fijar de forma sólida el conjunto de receptáculo en su posición integrada al barandal de la cubierta del velero, pero por estar solo atornillado esta unión puede ser desatornillada por abajo. Ahora, continuado entornillando el tornillo sin cabeza acaba empujando el conjunto de receptáculo hacia arriba, pues la rosca en su lado superior choca con el perfil U de laton soldado al pedestal y asi el tornillo, soprtado por el aluminio de la estructura de la cubierta empuja el conjunto hacia arriba! Por otro lado el conjunto en su lado posterior esta en contacto con la superficie de chapa de madera del barandal, que ha sido realizado de tal forma que permita que le conjunto de receptáculo se deslize en su movimiento hacia arriba. Las fisuras entre la pared interior del barandal y el conjunto del receptáculo son tapadas usando el espray de "Plastico" de Kontakt Chemie, un espray usado para impermeablizar circuitos electrónicos. este espray es aplicado a todas las fisuras entre el conjunto de receptáculo y su entorno, como también entrela luz y el receptáculo. Si esta impermeabilisación resultara danada, esto afectaría la humedad ambiental dentro del receptáculo y el sensor usado registraría un cambio de la humedad ambiental y así me daría reporte de revisar la impermeabilidad del conjunto de receptáculo y luz"! Se que es una locura, pero me parece genial. El sensor SHT21 se la empresa Sensirion, una nueva e inovativa empresa que resultó del ámbito de la prestigiosa universidad ETH Zurich, fuera de medir la temperatura, mide la humedad y da los datos completamente calibrados y de forma digital. No existen experiencias de un uso como el previsto, lo que hace de este velero lo mas avanzado en cuentión de electrónica!
--------------------
Saludos Hellmut
Saludos Hellmut
- Genaro Miranda
- Incondicional
- Mensajes: 896
- Registrado: Mar Feb 09, 2010 1:57 am
- Ubicación: Mexico,D.F.
- Contactar:
Re: Construción Voilier según planos
Hola otras vez........escribe tan largo casi me da sueño. 

- Hellmut1956
- Miembro Leal
- Mensajes: 1305
- Registrado: Sab Nov 29, 2008 2:06 pm
- Ubicación: Mammendorf, Alemania
Re: Construción Voilier según planos
Así es amigo, pero tu eres una prueba del porque! Como puedes ver, siempre me quedan preguntas a tus mensajes. Datos incompletos son de poca ayuda! Hemos visto en un hilo en er foro de modelismo naval aquí en Alemania, se llama Torno para novatos, como entorno al uso del torno hay tantas preguntas y falta de entendimiento que los expertos ni se las imaginan. Así ese hilo se volvió bien extenso! Por eso, cuando quieras sacar provecho a los temas bastante avanzados que aparecen y aparecerán en el próximo tiempo en este hilo, duerme y descanza para estar isto y preparado para digerir los datos! 

--------------------
Saludos Hellmut
Saludos Hellmut
- Hellmut1956
- Miembro Leal
- Mensajes: 1305
- Registrado: Sab Nov 29, 2008 2:06 pm
- Ubicación: Mammendorf, Alemania
Re: Construción Voilier según planos
Bueno amigos, me acaban de llegar las partes de aluminio que habia comprado para hacer las cajaspara las baterías en el casco y los cartuchos con sus sendos tambores parael control de las velas de mi velero. ya había escrito algo al respecto el sábado 29 del 2008 en este hilo.
Entonces mis planes eran poner las 12 baterías de LiFePo4 en una sola caja de baterías en el casco, detalles se pueden ver en el mensaje que publique entonces.
Desde entonces he desarollado un concepto nuevo para el control de las velas de mi velero que me permite cambiar el largo de los hilos de control de las velas por sobre un largo casi ilimitado y que en mi caso serán casi 1,9 metros!
El resultado es que usaré 2 motores de paso, que restarán cada una sobre una de las dos cajas de baterías, permitiendome un control completamente independiente de cada vela y a la vez, gracias a la electrónica, desde los controles de la emisora no cambiará nada,ya que esta libertad será usadada para permitir el trimm del control de las velas.
Aquí unos esquemas rudimentarios que muestran las 2 cajas de baterías en el casco. Un resultado de este cambio es que el punto de gravedad del velereo estará mucho mas abajo que antes!

Este gráfico muestra el antiguo y el nuevo concepto. Arriba se puede ver como habia previsto poner las 12 baterías en una caja detras del mástil y el motor de paso al frente. Resulta que esto no ayuda a resolver que hasta ahora el peso del casco está demasiado atras!
La imagen abajo muestra con reduzco la altura de la caja de baterías y como pongo la mitad, 6 baterías adelante y debajo del motor de paso. Desde entonces mi concepto ha sido refinado aún mas, previendo un segundo motor de paso montado de igual forma sobre la segunda caja de baterías.
Entre las cajas de baterías se tiene una vista lateral del cartucho con el tambor para el hilo de control de la vela. En el concepto actual preveo poner allí de estos cartuchos, uno conectado a cada uno de los motores de paso.

Este segundo esquema nos da una vista de enfrente del cartucho con el tambor en su posición en el casco. Como pueden ver este concepto requiere que los motores de paso estén montados lo suficientemente altos, para que el tambor con un diámetro de 150mm quepa en el casco. esto es lo genial, y perdonen mi orgullo, de mi concepto de usar como winche un motor de paso! Por lo general lo que prohibe usar tambores grandes en un velero para lograr mover el hilo de control por longitudes prolongadas, es que el torque es proporcional al radio del tambor. Cuanto mas grande el radio, mayor el torque que el motor tiene que proveer, para poder contrarestar la fuerza del viento sobre la vela. Así esto limita la longitud de hilo que se puede mover sin que el viento acabe teniendo mas fuerza que el motor.
En mi concepto usando un motor de paso, el motor de paso tiene mas torque disponible cuanto mas lento se mueva. Así, cuando mas grande el diámetro del tambor, mas lento se requiere que el motor gire y mas torque tiene el motor para contener las fuerzas del viento!

Aquí la imagen del cartucho que contiene un tambor! También aquí he podido refinar el diseno! En vez de usar para las paredes laterales placas de aluminio de 5mm de grosor, resultando en la necesidad de hacer una pieza que vaya entre las 2 placas de aluminio como sepuede ver en la imagen lateral del cartucho, ahora hago el cartucho con placas de aluminio de 10mm de grosor!
Esto es el resultado de ayudas y recomendaciones de foreros en los mas diversos foros y la pregunta que presentado en este foro relacionado a la mesa giratoria que pueden ller en el subforo de herramientas!

Acabé comprandome la mesa giratoria que ven en la imagen y que tiene el nombre de RTU 165 en las páginas de web de la empresa Optimum-Maschinen.de con todos sus accesorios! Me llega el martes o miercoles. Esta mesa me permite, montada sobre la mesa de coordenadas de mi fresa BF20L de la misma empresa, fresar superficies en forma de círculo! Así puedo fresar las placas de aluminio tal como lo muestra el dibujo!
Hoy al medio día me llego el paquete con las partes de aluminio, tanto para los 2 cartuchos, consistiendo de 1 placa de aluminio de 200x800x10mm y de 2 partes circulares de 150mm de diámtro por 40mm de grosor:

Aquí ven el paquete con un peso de 13kg!

Aquí pueden ver las piezas para mecanizar los tambores que irán dentro de sus sendos cartuchos. Lo que tengo pensado hacer es hacer un flanch adaptador que me permita poner el plato de torno de 165mm de diámetro en mi torno Quantum D210x400. El plato de torno original solo sirver para partes hasta un diámetro de 100mm, aumque el espacio disponible en el torno permite mecanizar partes de un diámetro de 200mm. Estoy conciente que usando este plato de torno tanto mas grande en mi torno no voy a mecanizar partes por ejemplo de acero de diámetros tan grandes para evitar estresar la maquinaria con torques excesivos! Pero mecanizar las partes con un diámetro de 150mm mostradas aquí no debereían representar un problema.

Finalmente aquí ven 3 placas de aluminio, la mas grande abajo es la que usaré para hacer los cartuchos. Las placas por encima son para hacer las cajas de baterías!

Ahora a los progresos en la construcción de las cajas de baterías. El primer paso que hago, porque se los problemas que tengo en hacer las adaptaciones, es crear una plantilla de madera barata y tratar de adaptarla a lo mejor de mis habilidades al interior del casco. Como pueden ver el resultado actual deja mucho de desear! Pero mi intención es que usando esta plantilla, y equivalentes para las otras paredes de las cajas de baterías, puede ir adaptandolas hasta lograr la forma perfecta que entonces usaré para definir las formas de la placa correspondiente de aluminio. Creo que con la mesa de coordenados y la mesa giratoria me será posible fresar de forma manual la placa para que tenga la forma perfecta.
El segundo provecho de esto es que voy refinando mi entendimiento de los detalles, logrando así en el curso de la construcción identificar todos los problemas a considerar! Os puede decir que el número de problemas fatales que voy descubriendo en el curso de estas labores es muy significante. Gracias al procedimiento de usar plantillas la pérdida hasta este momento es nula, pues el uso de plantillas es para poder hacer las modificaciones y ver sus repercuciones, recién creando la parte final, cuando la plantilla confirme lo correcto!

Esta imagen muestra el plomo adicional que fundido e introducido en el casco. este plomo lo introducí, hasta que una de las imitaciones de las baterías reales estuviera restando sobre la superficie de plomo en una posición 100% horizontal. Así puedo identificar de forma empírica donde hacer la perforación de 6mm de diámetro en la placa de atras mostrada aquí.Pueden ver la línea vertical que he diujado en la plantilla y que representa el centro del casco, definiendo así donde poner la primera batería. Ademas pueden ver en la imagen los puntos de fijación que había creado para fijar el motor de paso en su posición antigua. Ahora el motor de paso estará fijado en la placa horizontal que cubrirá cada una de los cajas de baterías.

Aquí pueden ver una imitación de madera de las baterías que utilizaré en el velero, serán 12 en total, repartidas 6 y 6 en las dos cajas. Ahora haré la segunda plantilla de madera para la pared delantera de esta caja de baterías, pudiendo usar la imitación de baterías para saber la posición exacta de la pared delantera en relación a la de atras!

Aquí pueden ver una batería real y una imitación. Hay varias razones por las cuales he decidido usar replicas de las baterías y no la baterías mismas en esta fase de la construcción de mi velero.
La primera razón son los costos. Una batería cuesta 34,90 Euros, representando 12 de ellas una iversión muy sustanciosa. El almacenar estas baterías por sobre un tiempo de probablemente anos antes de usarlas realmente resultaría, aún con un buen tratamiento de las baterías, en una perdida de la expectativa de vida útil de esas baterías.
La segunda razón es el peligro en usar estas baterías en esta fase. cada batería tiene una capacidad de 16Ah y tranquilamente puede surtir 10C de corriente. Para refrescar, 1C dice que la corriente en A es igual al valor de la capacidad del la batería en Ah. en el caso de mis baterías de 16Ah, significa que en caso de cortocircuito puede fluir una corriente superior a los 160A! Creo que no requiere mucha fantasía para imaginarse las consecuencias!
Este segundo aspecto también se refleja en mi diseno de las cajas de baterías.

Aquí un dibujo de como las baterías son fijadas en la caja de baterías. Como pueden ver, estas baterías tienen en sus polos una rosca M6. Así puedo usar esta rosca para fijar las baterías en su posición en la caja de baterías. Ya me he expresado en este mensaje sobre como encuentro la posición de la perforación en la placa de aluminio que va a reemplazar las plantillas que estoy generando. Esta imagen muestra una de varias cosas que hago para seguridad adicional. La imagen muestra como tengo previsto mecanizar usando mi torno piezas de plástico de 40mm de diámetro y que aplico de ambas partes a las placas de aluminio que estoy definiendo con las plantillas mostradas arriba, para hacer imposible que los polos de las baterías entren en contacto con el aluminio de las paredes de la caja de baterías. También pueden ver que el tornillo M6 que uso para fijar cada batería en su posición en la caja de baterías no podran entrar en contacto con el aluminio. Crear estas superficies circulares en las paredes de la caja de baterías es otro de los usos de la mesa giratoria que he comprado. Es también la razón por la cual he decidido usar placas de aluminio de 10mm de grosor! La diferencia de precio entre las placas de aluminio de 10mm y de 5mm de grosor es tan reducida que esto no influye como factor negativo en esta decisión! Los 10 mm de grosor me dan amplio espacio para mecanizar las placas e introducir las piezas plásticas quedando sus superficies a la altura de la placa de aluminio.
Pero hay otras razónes para usar placas de aluminio de este grosor. Tengo que preveer cables para conectar los polos de las baterías individuales de tal forma, que en su conjunto formen un Pack de baterías de 12 en serie. Como recuerdo, requiero tantas baterías, porque las baterías cuando lleguen a vacías en suma aún tienen que proveeer los 24VDc que requiero para operar los frenos de los motores de paso, teniendo al mismo tiempo la ventaja de tener una tensión lo mas alta posible a aplicar a los motores de paso para un torque máximo de estos!
Ademas tengo que interconectar las baterías de tal forma, que el balancer del cargador pueda balancear las cargas de cada una de las 12 baterías del pack! El cargador de las baterías que uso es el de Akkumatik.de, donde estoy a punto de traducir los textos tanto del sitio de internet, como el de la pantalla de cargador al Espanol, haciendo así este cargador de baterías disponible en Espanol para aquellos de habla Hispana!
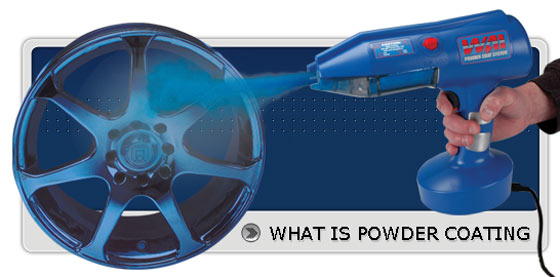
Y como en todo soy y gozo siendo extremo he previsto cosas mas para la seguridad de las baterías y de la alimentación eléctrica del velero. he adquirido este sistema para la aplicación de "powder coating" capa de plástico partiendo de polvo! Para este sistema vuelvo a poder aprovechar el tener mi horno de reflow para la electrónica. este sistema aplica una capa de polvo plástico a las sperficies de aluminio de las cajas de baterías del velero. Para eso se aplica la tierra a la placa de aluminio y la pistola tiene 12VDC. Las partes de polvo son cargadas electricamente positivo, siendo así atraidas electricamente a las placas de aluminio. Estas placas de aluminio entonces las meto en mi horno, calentándolas a 200 grados centígrados fundiendo así las partículas de polvo plástico y creando un cubrimiento de plástico que aislará electricamente las placas de aluminio evitando así posibles cortocircuitos acidentales. Como estas placas de aluminio serán atornilladas en sus posiciones, y porque la capa de plástico será de un color rojo como de bomberos, si llegan a ocurrir rasgones en la superficie, el color permite ver esto y así poder sacar las placas para repararlas. Como mi hermano llega de Méxiko afines de mes me traerá el sistema que me compro en los Estados Unidos por solo 149.- USD!
Entonces mis planes eran poner las 12 baterías de LiFePo4 en una sola caja de baterías en el casco, detalles se pueden ver en el mensaje que publique entonces.
Desde entonces he desarollado un concepto nuevo para el control de las velas de mi velero que me permite cambiar el largo de los hilos de control de las velas por sobre un largo casi ilimitado y que en mi caso serán casi 1,9 metros!
El resultado es que usaré 2 motores de paso, que restarán cada una sobre una de las dos cajas de baterías, permitiendome un control completamente independiente de cada vela y a la vez, gracias a la electrónica, desde los controles de la emisora no cambiará nada,ya que esta libertad será usadada para permitir el trimm del control de las velas.
Aquí unos esquemas rudimentarios que muestran las 2 cajas de baterías en el casco. Un resultado de este cambio es que el punto de gravedad del velereo estará mucho mas abajo que antes!

Este gráfico muestra el antiguo y el nuevo concepto. Arriba se puede ver como habia previsto poner las 12 baterías en una caja detras del mástil y el motor de paso al frente. Resulta que esto no ayuda a resolver que hasta ahora el peso del casco está demasiado atras!
La imagen abajo muestra con reduzco la altura de la caja de baterías y como pongo la mitad, 6 baterías adelante y debajo del motor de paso. Desde entonces mi concepto ha sido refinado aún mas, previendo un segundo motor de paso montado de igual forma sobre la segunda caja de baterías.
Entre las cajas de baterías se tiene una vista lateral del cartucho con el tambor para el hilo de control de la vela. En el concepto actual preveo poner allí de estos cartuchos, uno conectado a cada uno de los motores de paso.

Este segundo esquema nos da una vista de enfrente del cartucho con el tambor en su posición en el casco. Como pueden ver este concepto requiere que los motores de paso estén montados lo suficientemente altos, para que el tambor con un diámetro de 150mm quepa en el casco. esto es lo genial, y perdonen mi orgullo, de mi concepto de usar como winche un motor de paso! Por lo general lo que prohibe usar tambores grandes en un velero para lograr mover el hilo de control por longitudes prolongadas, es que el torque es proporcional al radio del tambor. Cuanto mas grande el radio, mayor el torque que el motor tiene que proveer, para poder contrarestar la fuerza del viento sobre la vela. Así esto limita la longitud de hilo que se puede mover sin que el viento acabe teniendo mas fuerza que el motor.
En mi concepto usando un motor de paso, el motor de paso tiene mas torque disponible cuanto mas lento se mueva. Así, cuando mas grande el diámetro del tambor, mas lento se requiere que el motor gire y mas torque tiene el motor para contener las fuerzas del viento!

Aquí la imagen del cartucho que contiene un tambor! También aquí he podido refinar el diseno! En vez de usar para las paredes laterales placas de aluminio de 5mm de grosor, resultando en la necesidad de hacer una pieza que vaya entre las 2 placas de aluminio como sepuede ver en la imagen lateral del cartucho, ahora hago el cartucho con placas de aluminio de 10mm de grosor!
Esto es el resultado de ayudas y recomendaciones de foreros en los mas diversos foros y la pregunta que presentado en este foro relacionado a la mesa giratoria que pueden ller en el subforo de herramientas!

Acabé comprandome la mesa giratoria que ven en la imagen y que tiene el nombre de RTU 165 en las páginas de web de la empresa Optimum-Maschinen.de con todos sus accesorios! Me llega el martes o miercoles. Esta mesa me permite, montada sobre la mesa de coordenadas de mi fresa BF20L de la misma empresa, fresar superficies en forma de círculo! Así puedo fresar las placas de aluminio tal como lo muestra el dibujo!
Hoy al medio día me llego el paquete con las partes de aluminio, tanto para los 2 cartuchos, consistiendo de 1 placa de aluminio de 200x800x10mm y de 2 partes circulares de 150mm de diámtro por 40mm de grosor:

Aquí ven el paquete con un peso de 13kg!

Aquí pueden ver las piezas para mecanizar los tambores que irán dentro de sus sendos cartuchos. Lo que tengo pensado hacer es hacer un flanch adaptador que me permita poner el plato de torno de 165mm de diámetro en mi torno Quantum D210x400. El plato de torno original solo sirver para partes hasta un diámetro de 100mm, aumque el espacio disponible en el torno permite mecanizar partes de un diámetro de 200mm. Estoy conciente que usando este plato de torno tanto mas grande en mi torno no voy a mecanizar partes por ejemplo de acero de diámetros tan grandes para evitar estresar la maquinaria con torques excesivos! Pero mecanizar las partes con un diámetro de 150mm mostradas aquí no debereían representar un problema.

Finalmente aquí ven 3 placas de aluminio, la mas grande abajo es la que usaré para hacer los cartuchos. Las placas por encima son para hacer las cajas de baterías!

Ahora a los progresos en la construcción de las cajas de baterías. El primer paso que hago, porque se los problemas que tengo en hacer las adaptaciones, es crear una plantilla de madera barata y tratar de adaptarla a lo mejor de mis habilidades al interior del casco. Como pueden ver el resultado actual deja mucho de desear! Pero mi intención es que usando esta plantilla, y equivalentes para las otras paredes de las cajas de baterías, puede ir adaptandolas hasta lograr la forma perfecta que entonces usaré para definir las formas de la placa correspondiente de aluminio. Creo que con la mesa de coordenados y la mesa giratoria me será posible fresar de forma manual la placa para que tenga la forma perfecta.
El segundo provecho de esto es que voy refinando mi entendimiento de los detalles, logrando así en el curso de la construcción identificar todos los problemas a considerar! Os puede decir que el número de problemas fatales que voy descubriendo en el curso de estas labores es muy significante. Gracias al procedimiento de usar plantillas la pérdida hasta este momento es nula, pues el uso de plantillas es para poder hacer las modificaciones y ver sus repercuciones, recién creando la parte final, cuando la plantilla confirme lo correcto!

Esta imagen muestra el plomo adicional que fundido e introducido en el casco. este plomo lo introducí, hasta que una de las imitaciones de las baterías reales estuviera restando sobre la superficie de plomo en una posición 100% horizontal. Así puedo identificar de forma empírica donde hacer la perforación de 6mm de diámetro en la placa de atras mostrada aquí.Pueden ver la línea vertical que he diujado en la plantilla y que representa el centro del casco, definiendo así donde poner la primera batería. Ademas pueden ver en la imagen los puntos de fijación que había creado para fijar el motor de paso en su posición antigua. Ahora el motor de paso estará fijado en la placa horizontal que cubrirá cada una de los cajas de baterías.

Aquí pueden ver una imitación de madera de las baterías que utilizaré en el velero, serán 12 en total, repartidas 6 y 6 en las dos cajas. Ahora haré la segunda plantilla de madera para la pared delantera de esta caja de baterías, pudiendo usar la imitación de baterías para saber la posición exacta de la pared delantera en relación a la de atras!

Aquí pueden ver una batería real y una imitación. Hay varias razones por las cuales he decidido usar replicas de las baterías y no la baterías mismas en esta fase de la construcción de mi velero.
La primera razón son los costos. Una batería cuesta 34,90 Euros, representando 12 de ellas una iversión muy sustanciosa. El almacenar estas baterías por sobre un tiempo de probablemente anos antes de usarlas realmente resultaría, aún con un buen tratamiento de las baterías, en una perdida de la expectativa de vida útil de esas baterías.
La segunda razón es el peligro en usar estas baterías en esta fase. cada batería tiene una capacidad de 16Ah y tranquilamente puede surtir 10C de corriente. Para refrescar, 1C dice que la corriente en A es igual al valor de la capacidad del la batería en Ah. en el caso de mis baterías de 16Ah, significa que en caso de cortocircuito puede fluir una corriente superior a los 160A! Creo que no requiere mucha fantasía para imaginarse las consecuencias!
Este segundo aspecto también se refleja en mi diseno de las cajas de baterías.

Aquí un dibujo de como las baterías son fijadas en la caja de baterías. Como pueden ver, estas baterías tienen en sus polos una rosca M6. Así puedo usar esta rosca para fijar las baterías en su posición en la caja de baterías. Ya me he expresado en este mensaje sobre como encuentro la posición de la perforación en la placa de aluminio que va a reemplazar las plantillas que estoy generando. Esta imagen muestra una de varias cosas que hago para seguridad adicional. La imagen muestra como tengo previsto mecanizar usando mi torno piezas de plástico de 40mm de diámetro y que aplico de ambas partes a las placas de aluminio que estoy definiendo con las plantillas mostradas arriba, para hacer imposible que los polos de las baterías entren en contacto con el aluminio de las paredes de la caja de baterías. También pueden ver que el tornillo M6 que uso para fijar cada batería en su posición en la caja de baterías no podran entrar en contacto con el aluminio. Crear estas superficies circulares en las paredes de la caja de baterías es otro de los usos de la mesa giratoria que he comprado. Es también la razón por la cual he decidido usar placas de aluminio de 10mm de grosor! La diferencia de precio entre las placas de aluminio de 10mm y de 5mm de grosor es tan reducida que esto no influye como factor negativo en esta decisión! Los 10 mm de grosor me dan amplio espacio para mecanizar las placas e introducir las piezas plásticas quedando sus superficies a la altura de la placa de aluminio.
Pero hay otras razónes para usar placas de aluminio de este grosor. Tengo que preveer cables para conectar los polos de las baterías individuales de tal forma, que en su conjunto formen un Pack de baterías de 12 en serie. Como recuerdo, requiero tantas baterías, porque las baterías cuando lleguen a vacías en suma aún tienen que proveeer los 24VDc que requiero para operar los frenos de los motores de paso, teniendo al mismo tiempo la ventaja de tener una tensión lo mas alta posible a aplicar a los motores de paso para un torque máximo de estos!
Ademas tengo que interconectar las baterías de tal forma, que el balancer del cargador pueda balancear las cargas de cada una de las 12 baterías del pack! El cargador de las baterías que uso es el de Akkumatik.de, donde estoy a punto de traducir los textos tanto del sitio de internet, como el de la pantalla de cargador al Espanol, haciendo así este cargador de baterías disponible en Espanol para aquellos de habla Hispana!
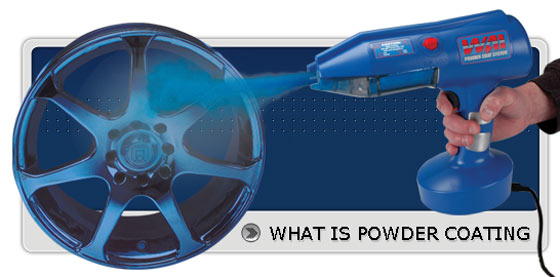
Y como en todo soy y gozo siendo extremo he previsto cosas mas para la seguridad de las baterías y de la alimentación eléctrica del velero. he adquirido este sistema para la aplicación de "powder coating" capa de plástico partiendo de polvo! Para este sistema vuelvo a poder aprovechar el tener mi horno de reflow para la electrónica. este sistema aplica una capa de polvo plástico a las sperficies de aluminio de las cajas de baterías del velero. Para eso se aplica la tierra a la placa de aluminio y la pistola tiene 12VDC. Las partes de polvo son cargadas electricamente positivo, siendo así atraidas electricamente a las placas de aluminio. Estas placas de aluminio entonces las meto en mi horno, calentándolas a 200 grados centígrados fundiendo así las partículas de polvo plástico y creando un cubrimiento de plástico que aislará electricamente las placas de aluminio evitando así posibles cortocircuitos acidentales. Como estas placas de aluminio serán atornilladas en sus posiciones, y porque la capa de plástico será de un color rojo como de bomberos, si llegan a ocurrir rasgones en la superficie, el color permite ver esto y así poder sacar las placas para repararlas. Como mi hermano llega de Méxiko afines de mes me traerá el sistema que me compro en los Estados Unidos por solo 149.- USD!
--------------------
Saludos Hellmut
Saludos Hellmut
- Hellmut1956
- Miembro Leal
- Mensajes: 1305
- Registrado: Sab Nov 29, 2008 2:06 pm
- Ubicación: Mammendorf, Alemania
Re: Construción Voilier según planos
Aquí os muestro una placa, que violando mis principios de hacer todo yo mismo he acabado comprando!

Esta placa implementa el circuito, como aparece en el sitio de internet de la empresa Linear Technology para su componente LT6802-1. Allí este circuito se utiliza para el monitoréo de las baterías de un coche eléctrico. Esta placa es parte del cargador de la empresa Akkumatik.de y tiene la función del balancéo de la baterías que componen un pack de baterías! Como recuerdo. En especial las baterías a base de litio requieren, para su seguro de vida pues tienden a quemarse o explotar si son usadas indebidamente, que todas las baterías de un pack tengan la misma carga y la misma tensión. Esta placa tiene la capacidad de balancear, lo que signifia igualar, las tensiones de las baterías de un pack con altísima precisión de hasta 12 baterías conectadas en serie. Yo me acabo de comprar ese cagador para las 12 baterías de LiFePO4 que conformarán el pack de baterías en mi velero! pero me compré una placa adicional para, modificando el programa en el controlador ATTiny44, un controlador AVR de Atmel que se puede programar con BASCOM, hacer de esta placa un sistema de monitoreo de las baterías en mi velero. Por 45,- Euros me pareció válido el comprar esta placa y no hacerla yo mismo. Pueden ver que es bastante compleja!
Los conectores grandes son para conectar los cables de cobre para el balanceo. El dispositivo a la izquierda arriba es la tan apreciada parte por mi, la LT6802-1, la parte por encima del conector derecho es el controlador Atmel Attiny44. El conector con el cable plano al borde derecho de la placa es donde la placa es conectada a la placa principal del cargador.

Esta placa implementa el circuito, como aparece en el sitio de internet de la empresa Linear Technology para su componente LT6802-1. Allí este circuito se utiliza para el monitoréo de las baterías de un coche eléctrico. Esta placa es parte del cargador de la empresa Akkumatik.de y tiene la función del balancéo de la baterías que componen un pack de baterías! Como recuerdo. En especial las baterías a base de litio requieren, para su seguro de vida pues tienden a quemarse o explotar si son usadas indebidamente, que todas las baterías de un pack tengan la misma carga y la misma tensión. Esta placa tiene la capacidad de balancear, lo que signifia igualar, las tensiones de las baterías de un pack con altísima precisión de hasta 12 baterías conectadas en serie. Yo me acabo de comprar ese cagador para las 12 baterías de LiFePO4 que conformarán el pack de baterías en mi velero! pero me compré una placa adicional para, modificando el programa en el controlador ATTiny44, un controlador AVR de Atmel que se puede programar con BASCOM, hacer de esta placa un sistema de monitoreo de las baterías en mi velero. Por 45,- Euros me pareció válido el comprar esta placa y no hacerla yo mismo. Pueden ver que es bastante compleja!
Los conectores grandes son para conectar los cables de cobre para el balanceo. El dispositivo a la izquierda arriba es la tan apreciada parte por mi, la LT6802-1, la parte por encima del conector derecho es el controlador Atmel Attiny44. El conector con el cable plano al borde derecho de la placa es donde la placa es conectada a la placa principal del cargador.
Última edición por Hellmut1956 el Mar Feb 22, 2011 6:52 pm, editado 1 vez en total.
--------------------
Saludos Hellmut
Saludos Hellmut
- Genaro Miranda
- Incondicional
- Mensajes: 896
- Registrado: Mar Feb 09, 2010 1:57 am
- Ubicación: Mexico,D.F.
- Contactar:
Re: Construción Voilier según planos
Tu fotos no aparece hellmult....... 

- Hellmut1956
- Miembro Leal
- Mensajes: 1305
- Registrado: Sab Nov 29, 2008 2:06 pm
- Ubicación: Mammendorf, Alemania
Re: Construción Voilier según planos
Hola amigos y gracias Genaro por indicarme ue lo foto no aparece. Ahora si la muestra, verdad!
Pues bien, finalmente uniendo cabos y así pudiendo anadir un poco al reporte paso a paso.
Como escribía en mi reporte del 19 de febrero estoy construyendo la primera de las dos cajas de baterías. Uso para estas cajas láminas de aluminio de 10mm de grosor, pues tengo que insertar en estas paredes partes mecanizadas en mi torno de plástico que evitan que el polo de la batería entre en contacto eléctrico con el aluminio,pudiendo así causar un corto en el que pueden fluir hasta 240ª de corriente.
Para los trabajos de preparación hago plantillas que finalmente reemplazaré usando las láminas de aluminio. Como primer intento use el perfil de la cuaderna mas cercana al lugar donde se pondrá la pared de la caja de baterías trasera. El resultado de esta primera labor lo pudieron ver en mi último mensaje, donde aparece una vista interior del casco con la pared cuboerta con una hoja de papel blanco. Como pueden ver allí el camino a recorrer es aún largo. En la foto que le sigue podían ver la madera que uso para la plantilla, de 5mm de grosor, solo la mitad de los 10mm de aluminio! Finalmente aparecía una foto con un ad elas falsas batería que construí. El resultado de esto fue que podía analizar la labor y saber que el punto crítico será la otra pareed de la caja de baterías, la de adelante, pues esta es mas pequeña y por lo tanto define la posición de las baterías en la caja! La próxima imagen de hoy

Muestra el resultado después de largos paseos con mi perro en los alrededores de nuestra casa durante los cuales reflexionaba sobre posibles formas de realizar mi objetivo y las implicaciones de estas deciciones. Es incrreible, se ve el resultado y casi que uno mismo no puede creer ue largo fue el camino para llegar allí!
En esta imagen pueden ver la plantilla, ahora pegando dos láminas de madera de 5mm de grosor usando el pegante Pattex que pienso usar para el laminado con chapa de madera de caoba y las mismas técnicas. El experimento resultó, lo que ya me da mas confianza en el uso de Pattex como pegante para la chapa de madera! Así estas paredes de la caja de baterías tienen un grosor de 10mm que exige tomar en consideración al adaptarlas al casco en 3 dimensiones.
Tambien pueden ver en esta imagen como tuve que adaptar la forma de las plantillas, pues aún estaban en el casco los apoyos del motor de paso que antes tenía instalado allí! También ven la cabeza hexagonal del tornillo con el cual fijo la primera batería de esta caja en su sitio.
Gracias a la alte resolución y nitidez de las imágenes de mi webcam est aimagen permite ver a ambos lados el soporte que pegue al casco donde se fijan los hilos que vienen del mástil lateralmente. Detrás del perfil en forma de L de aluminio color bronze se encuentra a cada lado una barra de aluminio de 180x30x5mm peganda al casco para pasar las fuerzas a este. Los perfiles integrados en el sistema de estanqueidad del casco y la cubierta sostienen el punto donde el mástil atravieza la cubierta. Tambien se puede ver como fije con perfiles de aluminio en forma de T las estructuras y el atornillamiento de estas!

Esta foto muestra lo mismo desde arriba. Teniendo como referencia la pared trasera de la caja de baterías, la cual tiene como referencia de su posición el plomo adicional que puse en el casco identifique la cuaderna mas próxima a la posición de la pared delantera usando la batería y realice la plantilla de esta pared en varias iteraciones hasta lograr una calidad adecuada.
Ahora hay que tener en mente que las paredes laterales de la caja de baterías y que se encuentra entre estas dos paredes en la imagen quiero realizar de tal forma que las baterías resten sobre una lámina de acero o de aluminio que se amolde a las baterías individuales. Entre esta lámina y la pared de madera del casco llenaré los espacios vacíos con plomo, sacando la forma de los espacios vacíos usando cera, y fundiendo asaí los cuerpos de plomo. Pero eso lo mostraré en su debido tiempo. Lo imprtante aquí es que tengo que la primera batería en tal posición, que se me posible realitzar mi objetivo como planeado. La razón es que quiero que el centro de gravedad del veleero este lo mas abajo posible!

Esta imagen creo que lo explica un poco. Es la plantilla de la pared delantera de la caja de baterías. La lámina de acero se amoladara a las baterías exteriores, permitiendo a la batería de mas abajo estar en un recipiente con perfil de medio círculo, de alli la lánima sube verticalmente hasta ir a formar una superficie de apoyo para las baterías que siguen arriba, lo mismo para los baterías del tercer nivel, de donde la lánima suber verticalmente hasta alcanzar la tapa de la caja de baterías. Así todo el espacio experior del casco estará completamente llenado de plomo permitiendo así usar todo el volumen paranar con plomo. El espacio ente las baterías lo sacaré usando cera y creando así por fundición sendos cuerpos de plomo que rellenan los espacios vacios. La tapa también sera una lámina de aluminio de 10mm de grosor sobre la cual restará el motor d epaso.
Pero volvamos al imagen anterior! Usando una balanza hidrostática primero me encargué de poner el casco en tal posicion que el nivel de agua este en una posición 100% horizontal. Solo así pude verificar que la batería en la caja entre las plantillas tenía una posición horizontal y céntrica en el casco, sacando así la información de donde hacer la perforación para el tornillo que fija la batería en su posición!
Luego saque las plantillas del casco, hice la perforación de 6mm de diámetro y lo verifiue en el casco. Ahoa volví a sacar las platillas y la batería del casco, aquí la imagen:
Como las plantillas estan atornilladas a la batería pude poner las imitaciones baterías entre ellas para encontrar la posición mas adecuada ahora reflejada en la imagen anterior! Las líneas y circulos que ven dibujadas en la pared delantera de la caja de baterías tienen una función importantísima para los trabajos posteriores!
Voy a usar mi programa de CAD gratuito presentado anteriormente aquí para construir allí la geometría que define la posición de las perforaciones paralas baterías en las paredes de las cajas debaterías. Así, cuando haga las perforaciones usando mi fresa BF20L de Optimum, usaré las coordenadas del diseno en el programa de CAD con referncia a la perforación de la batería de bien abajo . Así defino ue ese punto tenga las coordenadas (0/0) y saco las coordenadas de los otros puntos del programa de CAD. Recuerden que mi fresa tiene una pantalla digital que me indica las coordenadas de la mesa de coordenadas y la ertical a una centésima de milimetro!
Pero esto no solo tiene importancia para las perforaciones, sino tambien cuando mecanice las ranuras circulares usando mi flamante y nueva mesa rotiva:
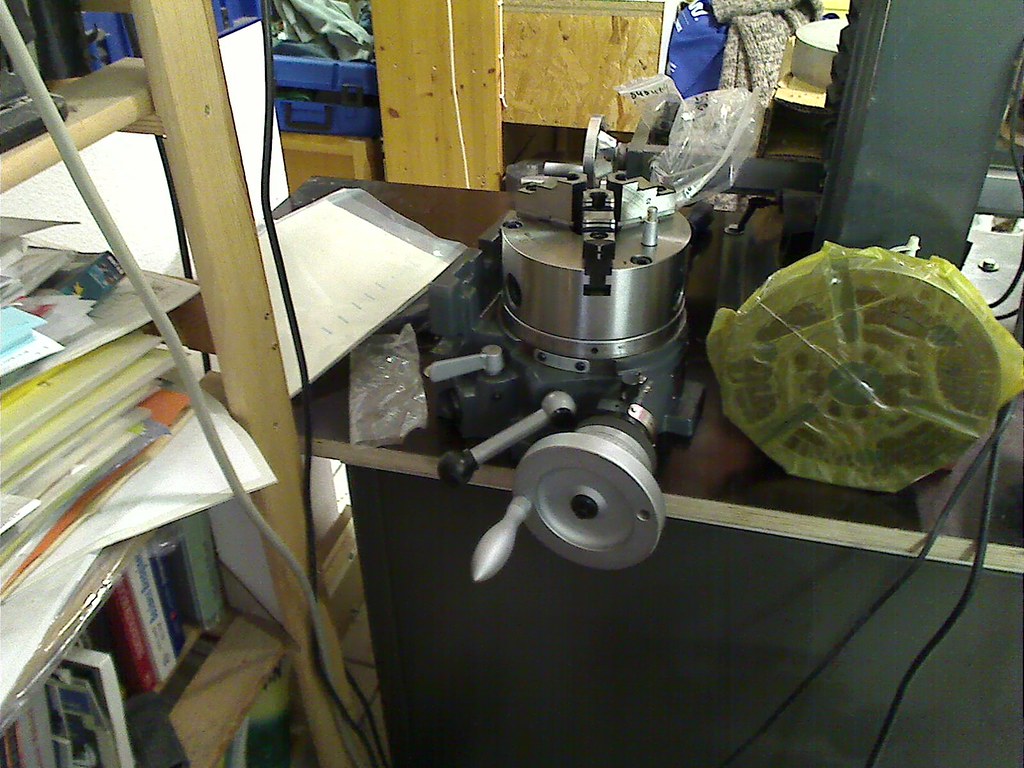
Esta mesa rotativa se monta sobre la mesa de coordenadas de la fresa fijando la lámina de aluminio usando el disco que ven aun forrado con el plástico. Las paredes de aluminio de 10mm de grosor las uso por varias razones:
1. Necesito integrar en las paredes las partes plásticas que evitan que los polos de las baterías toquen el aluminio creando así un corto.
2. Los polos de las baterías tienen ue ser conectados para crear un pack de 12 baterías en serie. Para este propósito he comprado una barra de cobre de 30x3mm de perfil. Con ese grosor estoy confidente que si llega haber un corto el conre no se calentará evitando así una posible causa de fuego!
3. Para el balanceo de las baterías, igualar las tensiones de las baterías individuales en el pack tengo que crear una toma en cada una de estas conexiones. Todo esto estará integrado en los 10mm de grosor de las paredes.
4. Las 6 baterías en cada una de las 2 cajas de baterías pesan enconjunto 3kg, mas el plomo! Tengo que asegurarme que este peso, esa masa estén sólidamente fijados en el casco. Las paredes de este grosor son un buen elemento para este propósito!
Bueno amigos hasta aquí hoy!
Pues bien, finalmente uniendo cabos y así pudiendo anadir un poco al reporte paso a paso.
Como escribía en mi reporte del 19 de febrero estoy construyendo la primera de las dos cajas de baterías. Uso para estas cajas láminas de aluminio de 10mm de grosor, pues tengo que insertar en estas paredes partes mecanizadas en mi torno de plástico que evitan que el polo de la batería entre en contacto eléctrico con el aluminio,pudiendo así causar un corto en el que pueden fluir hasta 240ª de corriente.
Para los trabajos de preparación hago plantillas que finalmente reemplazaré usando las láminas de aluminio. Como primer intento use el perfil de la cuaderna mas cercana al lugar donde se pondrá la pared de la caja de baterías trasera. El resultado de esta primera labor lo pudieron ver en mi último mensaje, donde aparece una vista interior del casco con la pared cuboerta con una hoja de papel blanco. Como pueden ver allí el camino a recorrer es aún largo. En la foto que le sigue podían ver la madera que uso para la plantilla, de 5mm de grosor, solo la mitad de los 10mm de aluminio! Finalmente aparecía una foto con un ad elas falsas batería que construí. El resultado de esto fue que podía analizar la labor y saber que el punto crítico será la otra pareed de la caja de baterías, la de adelante, pues esta es mas pequeña y por lo tanto define la posición de las baterías en la caja! La próxima imagen de hoy

Muestra el resultado después de largos paseos con mi perro en los alrededores de nuestra casa durante los cuales reflexionaba sobre posibles formas de realizar mi objetivo y las implicaciones de estas deciciones. Es incrreible, se ve el resultado y casi que uno mismo no puede creer ue largo fue el camino para llegar allí!
En esta imagen pueden ver la plantilla, ahora pegando dos láminas de madera de 5mm de grosor usando el pegante Pattex que pienso usar para el laminado con chapa de madera de caoba y las mismas técnicas. El experimento resultó, lo que ya me da mas confianza en el uso de Pattex como pegante para la chapa de madera! Así estas paredes de la caja de baterías tienen un grosor de 10mm que exige tomar en consideración al adaptarlas al casco en 3 dimensiones.
Tambien pueden ver en esta imagen como tuve que adaptar la forma de las plantillas, pues aún estaban en el casco los apoyos del motor de paso que antes tenía instalado allí! También ven la cabeza hexagonal del tornillo con el cual fijo la primera batería de esta caja en su sitio.
Gracias a la alte resolución y nitidez de las imágenes de mi webcam est aimagen permite ver a ambos lados el soporte que pegue al casco donde se fijan los hilos que vienen del mástil lateralmente. Detrás del perfil en forma de L de aluminio color bronze se encuentra a cada lado una barra de aluminio de 180x30x5mm peganda al casco para pasar las fuerzas a este. Los perfiles integrados en el sistema de estanqueidad del casco y la cubierta sostienen el punto donde el mástil atravieza la cubierta. Tambien se puede ver como fije con perfiles de aluminio en forma de T las estructuras y el atornillamiento de estas!

Esta foto muestra lo mismo desde arriba. Teniendo como referencia la pared trasera de la caja de baterías, la cual tiene como referencia de su posición el plomo adicional que puse en el casco identifique la cuaderna mas próxima a la posición de la pared delantera usando la batería y realice la plantilla de esta pared en varias iteraciones hasta lograr una calidad adecuada.
Ahora hay que tener en mente que las paredes laterales de la caja de baterías y que se encuentra entre estas dos paredes en la imagen quiero realizar de tal forma que las baterías resten sobre una lámina de acero o de aluminio que se amolde a las baterías individuales. Entre esta lámina y la pared de madera del casco llenaré los espacios vacíos con plomo, sacando la forma de los espacios vacíos usando cera, y fundiendo asaí los cuerpos de plomo. Pero eso lo mostraré en su debido tiempo. Lo imprtante aquí es que tengo que la primera batería en tal posición, que se me posible realitzar mi objetivo como planeado. La razón es que quiero que el centro de gravedad del veleero este lo mas abajo posible!

Esta imagen creo que lo explica un poco. Es la plantilla de la pared delantera de la caja de baterías. La lámina de acero se amoladara a las baterías exteriores, permitiendo a la batería de mas abajo estar en un recipiente con perfil de medio círculo, de alli la lánima sube verticalmente hasta ir a formar una superficie de apoyo para las baterías que siguen arriba, lo mismo para los baterías del tercer nivel, de donde la lánima suber verticalmente hasta alcanzar la tapa de la caja de baterías. Así todo el espacio experior del casco estará completamente llenado de plomo permitiendo así usar todo el volumen paranar con plomo. El espacio ente las baterías lo sacaré usando cera y creando así por fundición sendos cuerpos de plomo que rellenan los espacios vacios. La tapa también sera una lámina de aluminio de 10mm de grosor sobre la cual restará el motor d epaso.
Pero volvamos al imagen anterior! Usando una balanza hidrostática primero me encargué de poner el casco en tal posicion que el nivel de agua este en una posición 100% horizontal. Solo así pude verificar que la batería en la caja entre las plantillas tenía una posición horizontal y céntrica en el casco, sacando así la información de donde hacer la perforación para el tornillo que fija la batería en su posición!
Luego saque las plantillas del casco, hice la perforación de 6mm de diámetro y lo verifiue en el casco. Ahoa volví a sacar las platillas y la batería del casco, aquí la imagen:

Como las plantillas estan atornilladas a la batería pude poner las imitaciones baterías entre ellas para encontrar la posición mas adecuada ahora reflejada en la imagen anterior! Las líneas y circulos que ven dibujadas en la pared delantera de la caja de baterías tienen una función importantísima para los trabajos posteriores!
Voy a usar mi programa de CAD gratuito presentado anteriormente aquí para construir allí la geometría que define la posición de las perforaciones paralas baterías en las paredes de las cajas debaterías. Así, cuando haga las perforaciones usando mi fresa BF20L de Optimum, usaré las coordenadas del diseno en el programa de CAD con referncia a la perforación de la batería de bien abajo . Así defino ue ese punto tenga las coordenadas (0/0) y saco las coordenadas de los otros puntos del programa de CAD. Recuerden que mi fresa tiene una pantalla digital que me indica las coordenadas de la mesa de coordenadas y la ertical a una centésima de milimetro!
Pero esto no solo tiene importancia para las perforaciones, sino tambien cuando mecanice las ranuras circulares usando mi flamante y nueva mesa rotiva:
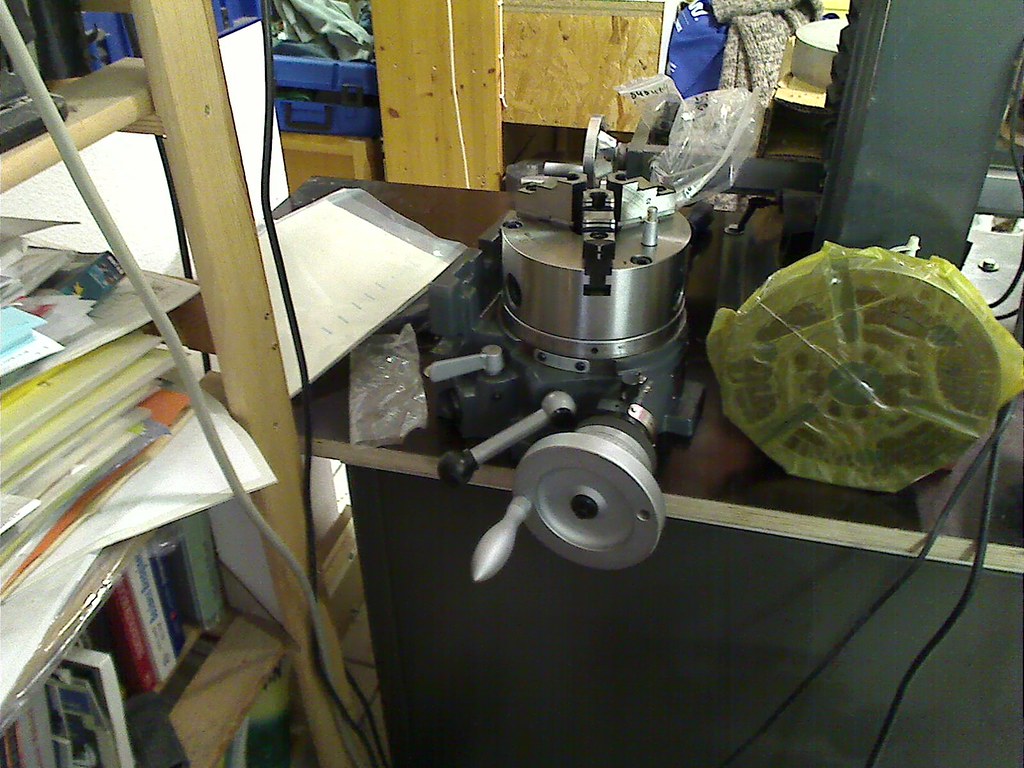
Esta mesa rotativa se monta sobre la mesa de coordenadas de la fresa fijando la lámina de aluminio usando el disco que ven aun forrado con el plástico. Las paredes de aluminio de 10mm de grosor las uso por varias razones:
1. Necesito integrar en las paredes las partes plásticas que evitan que los polos de las baterías toquen el aluminio creando así un corto.
2. Los polos de las baterías tienen ue ser conectados para crear un pack de 12 baterías en serie. Para este propósito he comprado una barra de cobre de 30x3mm de perfil. Con ese grosor estoy confidente que si llega haber un corto el conre no se calentará evitando así una posible causa de fuego!
3. Para el balanceo de las baterías, igualar las tensiones de las baterías individuales en el pack tengo que crear una toma en cada una de estas conexiones. Todo esto estará integrado en los 10mm de grosor de las paredes.
4. Las 6 baterías en cada una de las 2 cajas de baterías pesan enconjunto 3kg, mas el plomo! Tengo que asegurarme que este peso, esa masa estén sólidamente fijados en el casco. Las paredes de este grosor son un buen elemento para este propósito!
Bueno amigos hasta aquí hoy!
--------------------
Saludos Hellmut
Saludos Hellmut
- Genaro Miranda
- Incondicional
- Mensajes: 896
- Registrado: Mar Feb 09, 2010 1:57 am
- Ubicación: Mexico,D.F.
- Contactar:
Re: Construción Voilier según planos
Ayyyyyy!!! Caray! las fotos se ve como tamaño del monitor.....asi me gusta. 

- Hellmut1956
- Miembro Leal
- Mensajes: 1305
- Registrado: Sab Nov 29, 2008 2:06 pm
- Ubicación: Mammendorf, Alemania
Re: Construción Voilier según planos
Pues eso es por las quejas que eran muy pequenas!
--------------------
Saludos Hellmut
Saludos Hellmut
- Hellmut1956
- Miembro Leal
- Mensajes: 1305
- Registrado: Sab Nov 29, 2008 2:06 pm
- Ubicación: Mammendorf, Alemania
Re: Construción Voilier según planos
Bueno amigos
Los trabajos del Carina están progresando! A ver como lo contamos!
Empesemos por los trabajos con las réplicas de las baterías recargables. Resulta que estas de madera pesan 339 gramos menos que la batería recargable original, o sea en suma algo mas de 4kg adicionales, peso que necesito saber como esta situado para poder manterner el ojo puesto en repartir los pesos en el velero de tal forma que cabe flotando en la linea de flotación. la contribución de las baterías es muy considerable, son casi 6kg. Teniendo mi flamante mesa rotativa me decidí haver huecos longitudinales de 5x10x100mm, cada 60 Grados de los cilindros de madera y rellenarlos con pomo fundido.
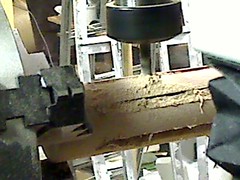
Aquí una vista de como la fresa con la mesa rotativa esta fresando los huecos longitudinales. Aquí otra vista:
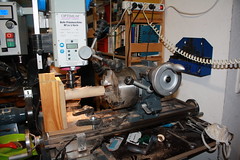
Como pueden ver me compre lamesa rotativa con el disco con garras de 165mm de diámetro. Durante este ejercicio pude aprender a usar mi mesa y descifrar cuales son los controles disponibles, donde se encuentran y como debo proceder a usar la mesa. Los errores que cometí son perdonables, pues en este trabajo no se requiere exactitud. En el subforo de herramientas he escrito algo al repescto.
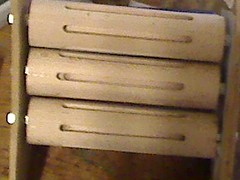
Aqui el resultado de los trabajos con la fresa. Se ven las réplicas de las baterías con los huecos longitudinales aún sin el plomo.

En esta imagen pueden apreciar como se ve el plomo fundido, pero aún sin limar en los huecos longitudinales.
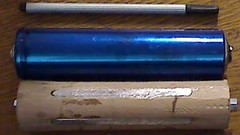
Aquí una foto de una de las réplicas con la batería recargable original junto a ella. He limado el plomo hasta reducir el peso para que fuera idéntico con los 487 gramos del original.resulto que en 5 de las réplicas no puse la suficiente cantidad de plomo, por lo que tuve que rellenar donde falto.
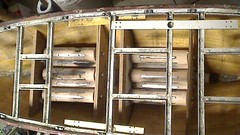
Aquí una imagen que muestra las 2 cajas de baterías en el casco con las 12 réplicas puestas en su sitio.
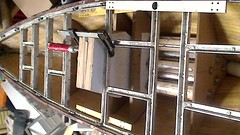
Aquí pueden ver las réplicas de los cartuchos que haré de aluminio y que contendrán los tambores con sus sendos hilos para controlar las velas. Las he fijado en la posición que equivale a la posición final.
No se imaginan que suerte he tenido. Resulta que todas estas construcciones en el casco caben en su sitio pero por casa de milímetros, lo que justifica el tremendo esfuerzo que he tenido que realizar creando tantas réplicas,tanto de las baterías, como de las plnachas que conformaran las cajas de baterías y los cartuchos para el control de las velas. Los datos que he recibido hasta este momento confirmaron lo siguiente y como resultado influyen muchísimo en como tengo que proceder los trabajos.
Como pueden ver las réplicas de los cartuchos para los tambores de control de las velas, mas arriba en este reporte ven esquemas que los explican, sobresalen el nivel del casco y entran en el nivel de la cubierta desmontable. De allí, y eso fue pura casualisdad que cuadrara, la superficie de atras del cartucho de atras tiene que quedar alineado con el perfil de "U" de la cubierta, por lo que resulta que la pared delantera de la caja trasera, que esta alineada con la del cartucho tiene que tener una posición así definida. Para lograr esto tuve que mover las cajas de las baterías hacia adelante por 1cm. Resulta que al otro lado el tubo que recibe el pie del mastil cuadra con un espacio de solo 5mm con el cartucho delantero. Hacia arriba los cartuchos solo tienes un espacio libre de 2mm contra la cubierta. Estas consideraciones no las había estudiado en detalle con anterioridad, pues muchos de los elementos de la construcción actual son el resultado de lo que he ido aprendiendo en el curso de la construcción y que me he estado ideando a razón de los mas múltiples estudios.
Aquí 2 imagenes mas que muestran que tanto suerte tuve!
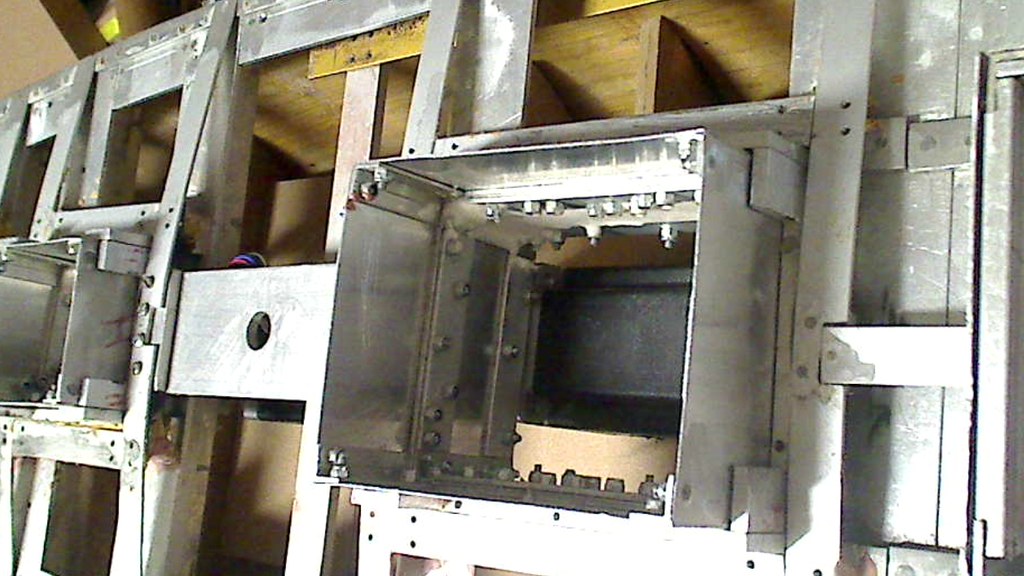
En esta foto ven un motor de paso y como no que ni un milímetro de espacio entre este y la edificación de la cubierta. El borde inferior casi que toca en motor de paso!
La última foto de hoy muestra la imagen del casco con la cubierta y las edificaciones con los motores de paso puestos en su lugar.
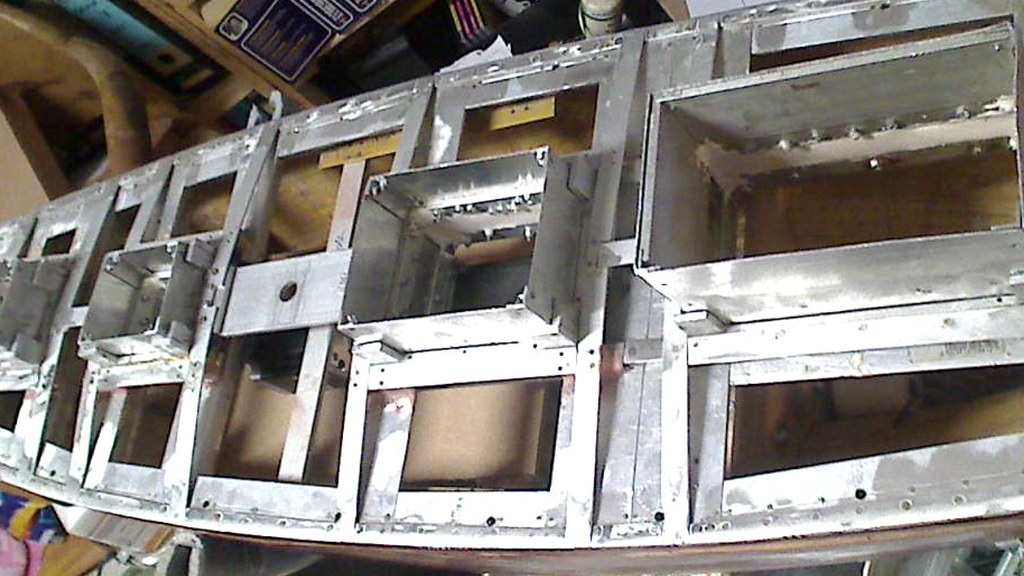
Los trabajos del Carina están progresando! A ver como lo contamos!
Empesemos por los trabajos con las réplicas de las baterías recargables. Resulta que estas de madera pesan 339 gramos menos que la batería recargable original, o sea en suma algo mas de 4kg adicionales, peso que necesito saber como esta situado para poder manterner el ojo puesto en repartir los pesos en el velero de tal forma que cabe flotando en la linea de flotación. la contribución de las baterías es muy considerable, son casi 6kg. Teniendo mi flamante mesa rotativa me decidí haver huecos longitudinales de 5x10x100mm, cada 60 Grados de los cilindros de madera y rellenarlos con pomo fundido.
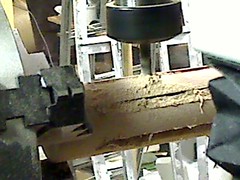
Aquí una vista de como la fresa con la mesa rotativa esta fresando los huecos longitudinales. Aquí otra vista:
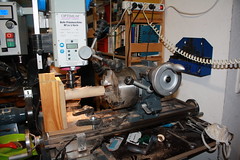
Como pueden ver me compre lamesa rotativa con el disco con garras de 165mm de diámetro. Durante este ejercicio pude aprender a usar mi mesa y descifrar cuales son los controles disponibles, donde se encuentran y como debo proceder a usar la mesa. Los errores que cometí son perdonables, pues en este trabajo no se requiere exactitud. En el subforo de herramientas he escrito algo al repescto.
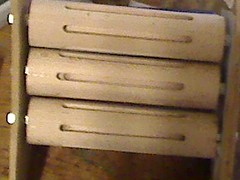
Aqui el resultado de los trabajos con la fresa. Se ven las réplicas de las baterías con los huecos longitudinales aún sin el plomo.

En esta imagen pueden apreciar como se ve el plomo fundido, pero aún sin limar en los huecos longitudinales.
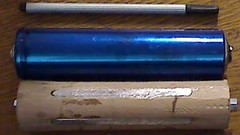
Aquí una foto de una de las réplicas con la batería recargable original junto a ella. He limado el plomo hasta reducir el peso para que fuera idéntico con los 487 gramos del original.resulto que en 5 de las réplicas no puse la suficiente cantidad de plomo, por lo que tuve que rellenar donde falto.
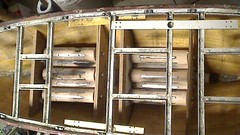
Aquí una imagen que muestra las 2 cajas de baterías en el casco con las 12 réplicas puestas en su sitio.
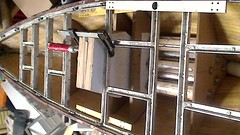
Aquí pueden ver las réplicas de los cartuchos que haré de aluminio y que contendrán los tambores con sus sendos hilos para controlar las velas. Las he fijado en la posición que equivale a la posición final.
No se imaginan que suerte he tenido. Resulta que todas estas construcciones en el casco caben en su sitio pero por casa de milímetros, lo que justifica el tremendo esfuerzo que he tenido que realizar creando tantas réplicas,tanto de las baterías, como de las plnachas que conformaran las cajas de baterías y los cartuchos para el control de las velas. Los datos que he recibido hasta este momento confirmaron lo siguiente y como resultado influyen muchísimo en como tengo que proceder los trabajos.
Como pueden ver las réplicas de los cartuchos para los tambores de control de las velas, mas arriba en este reporte ven esquemas que los explican, sobresalen el nivel del casco y entran en el nivel de la cubierta desmontable. De allí, y eso fue pura casualisdad que cuadrara, la superficie de atras del cartucho de atras tiene que quedar alineado con el perfil de "U" de la cubierta, por lo que resulta que la pared delantera de la caja trasera, que esta alineada con la del cartucho tiene que tener una posición así definida. Para lograr esto tuve que mover las cajas de las baterías hacia adelante por 1cm. Resulta que al otro lado el tubo que recibe el pie del mastil cuadra con un espacio de solo 5mm con el cartucho delantero. Hacia arriba los cartuchos solo tienes un espacio libre de 2mm contra la cubierta. Estas consideraciones no las había estudiado en detalle con anterioridad, pues muchos de los elementos de la construcción actual son el resultado de lo que he ido aprendiendo en el curso de la construcción y que me he estado ideando a razón de los mas múltiples estudios.
Aquí 2 imagenes mas que muestran que tanto suerte tuve!
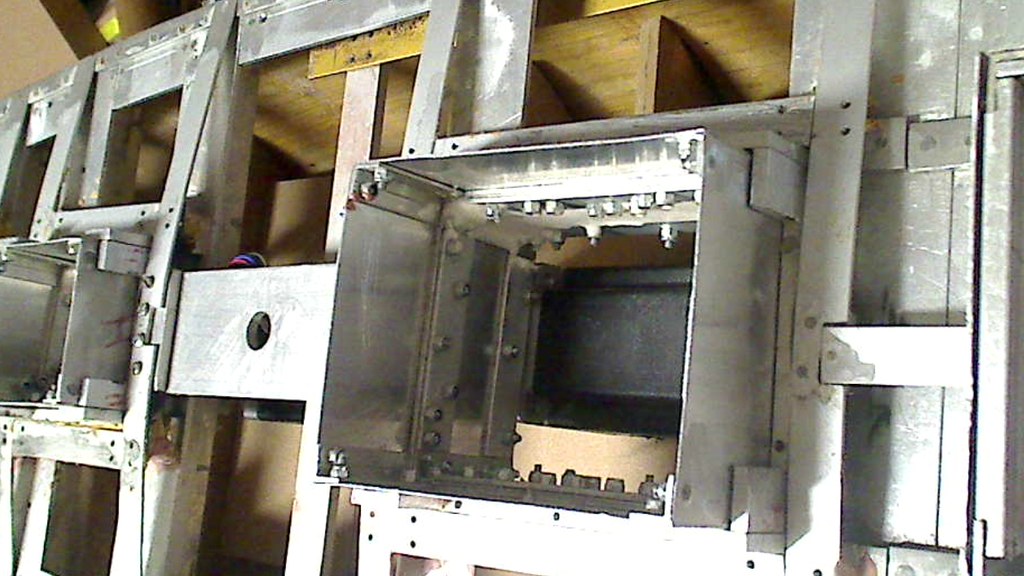
En esta foto ven un motor de paso y como no que ni un milímetro de espacio entre este y la edificación de la cubierta. El borde inferior casi que toca en motor de paso!
La última foto de hoy muestra la imagen del casco con la cubierta y las edificaciones con los motores de paso puestos en su lugar.
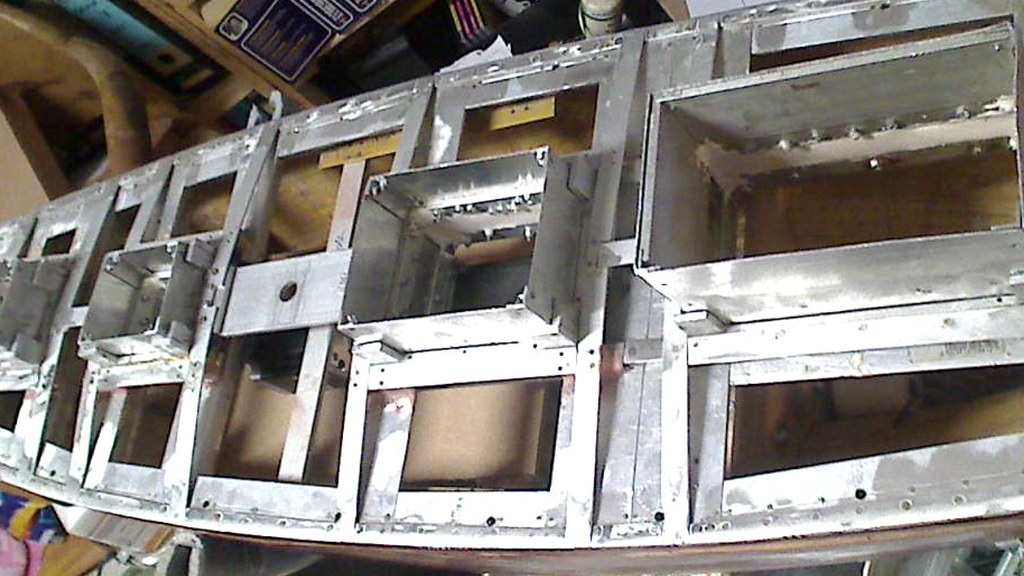
--------------------
Saludos Hellmut
Saludos Hellmut